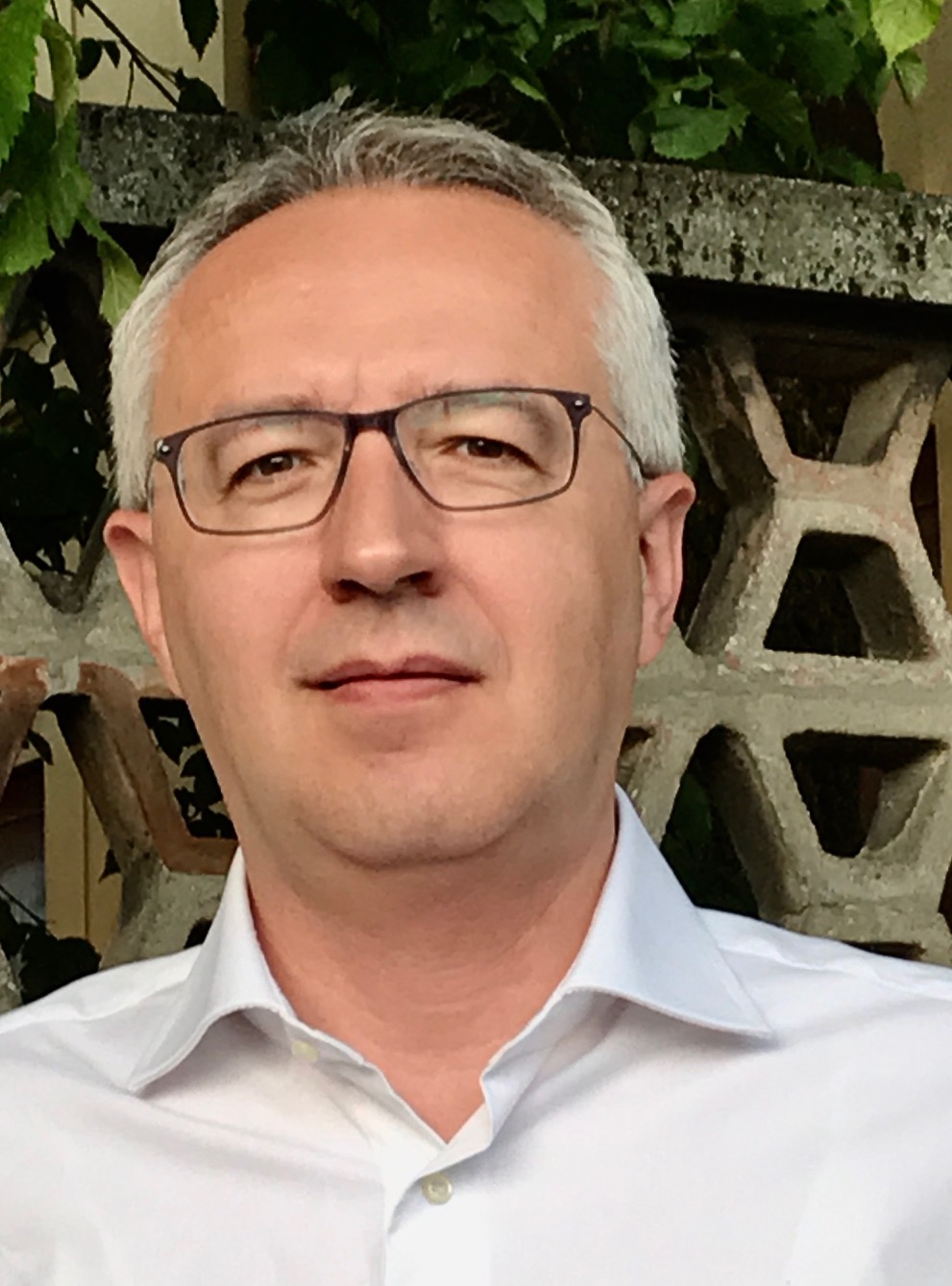 |
GIAN MARCO BIANCHI
Docente Interateneo Dipartimento di Ingegneria "Enzo Ferrari"
|
Home |
Curriculum(pdf) |
Didattica |
Pubblicazioni
2003
- Analysis of the HCCI combustion of a turbocharged truck engine using a stochastic reactor model
[Relazione in Atti di Convegno]
Montorsi, L.; Mauss, F.; Bianchi, G. M.; Bhave, A.; Kraft, M.
abstract
Homogeneous Charge Compression Ignition (HCCI) engines arouse great interest due to their high thermal efficiency and very low emissions of nitrogen oxides (NOx) and particulates. Critical issue of the HCCI combustion is the control of the engine since the combustion process is mostly dominated by chemical kinetics. Therefore the accurate assessment of the chemical kinetic is fundamental in numerical simulation of this kind of engines. Experimentally It has been demonstrated that even in HCCI engine the charge within the cylinder is not fully homogeneous, but many quantities, such as temperature, density and equivalence ratio, vary along the combustion chamber. These inhomogeneities influence the combustion process and yield the homogeneous reactor model to be not completely adequate to simulate HCCI combustion. This paper focuses on the use of a stochastic rector model in order to account for temperature inhomogeneities in the numerical simulation of the HCCI combustion. Moreover, the chemical kinetic code has been coupled to GT - Power Code, a 1-D fluid dynamics code, in order to accurately simulate the operation of a turbocharged truck engine.
2003
- Analysis of the HCCI combustion of a turbocharged truck engine using a stochastic reactor model
[Relazione in Atti di Convegno]
Montorsi, L.; Mauss, F.; Bianchi, G. M.; Bhave, A.; Kraft, M.
abstract
Homogeneous Charge Compression Ignition (HCCI) engines arouse great interest due to their high thermal efficiency and very low emissions of nitrogen oxides (NOx) and particulates. Critical issue of the HCCI combustion is the control of the engine since the combustion process is mostly dominated by chemical kinetics. Therefore the accurate assessment of the chemical kinetic is fundamental in numerical simulation of this kind of engines. Experimentally it has been demonstrated that even in HCCI engine the charge within the cylinder is not fully homogeneous, but many quantities, such as temperature, density and equivalence ratio, vary along the combustion chamber. These inhomogeneities influence the combustion process and yield the homogeneous reactor model to be not completely adequate to simulate HCCI combustion. This paper focuses on the use of a stochastic rector model in order to account for temperature inhomogeneities in the numerical simulation of the HCCI combustion. Moreover, the chemical kinetic code has been coupled to GT - Power Code, a 1-D fluid dynamics code, in order to accurately simulate the operation of a turbocharged truck engine.
2001
- Development of a Dynamic Model for Studying the 1st Generation of Common Rail Injectors for HSDI Diesel Engines
[Relazione in Atti di Convegno]
Bianchi, G. M.; Pelloni, S. F. P.; Filicori, F.; Milani, M.
abstract
The aim of this work is to investigate Common Rail injector behavior towards multiple injection strategies. A numerical model has been developed to simulate the electro-fluid-mechanic behavior of a Bosch mass production injector (standard injector) and validation against experiments has been performed. In order make the injector performing multiple injections, a deep investigation has been numerically carried out. The numerical study highlighted different area where injector may be improved with particular emphasis on electronic driving circuit. A new driving circuit concept, previously developed, has been successfully simulated showing promising fast-response capability for injector actuation.
2000
- Experimental and numerical investigation on the EGR system of a new automotive diesel engine
[Relazione in Atti di Convegno]
Mattarelli, E.; Bianchi, G. M.; Ivaldi, D.
abstract
In this paper an integrated experimental and numerical approach is applied to optimize a new 2.5l, four valve, turbocharged DI Diesel engine, developed by VM Motori. The study is focused on the EGR system. For this engine, the traditional dynamometer bench tests provided 3-D maps for brake specific fuel consumption and emissions as a function of engine speed and brake mean effective pressure. Particularly, a set of operating conditions has been considered which, according to the present European legislation, are fundamental for emissions. For these conditions, the influence of the amount of EGR has been experimentally evaluated. A computational model for the engine cycle simulation at full load has been built by using the WAVE code. The model has been set up against experiments, since an excellent agreement has been reached for all the relevant thermo-fluid-dynamic parameters. The simulation model has been used to gain a better insight on the EGR system operations. Furthermore, the influence of the most important geometric parameters (EGR valve seat diameter, intake manifold throttle diameter) on the amount of recycled gas for a few critical operating conditions has been investigated. Copyright © 2000 Society of Automotive Engineers, Inc.
2000
- Numerical study of the combustion chamber shape for common rail H.S.D.I. diesel engines
[Relazione in Atti di Convegno]
Bianchi, G. M.; Pelloni, P.; Corcione, F. E.; Mattarelli, E.; Bertoni, F. L.
abstract
The Common-rail injection system has allowed achieving a more flexible fuel injection control in DI-diesel engines by permitting a free mapping of the start of injection, injection pressure, rate of injection. All these benefits have been gained by installing this device in combustion chambers born to work with the conventional distributor and in-line-pump injection systems. Their design was aimed to improve air-fuel mixing and therefore they were characterized by the adoption of high-swirl ports and re-entrant bowls. Experiments have shown that the high injection velocities induced by common rail systems determine an enhancement of the air fuel mixing. By contrast, they cause a strong wall impingement too. The present paper aims to exploit a new configuration of the combustion chamber more suited to CR injection systems and characterized by low-swirl ports and larger bowl diameter in order to reduce the wall impingement. The goal is to achieve a higher air flow rate during induction as well as to reduce the fuel vapor wall impingement without compromising air-fuel mixing efficiency. This new combustion chamber configuration has been tested numerically and its performances have been compared to those of a H.S.D.I four valve diesel engine conventional combustion chamber. The analysis has been carried out by using a customized version of the CFD code KIVA3. Experimental results of the conventional combustion chamber have been used to validate the numerical models. The influence of the injection system configuration (i.e, hole numbers, inclination of the spray axis with respect cylinder head) on pressure cycle and NOx and soot engine-out emissions has been analyzed too. Computational results seem to indicate that the new combustion system concept may provide relevant benefits with respect to engine-out emissions without reducing engine performance. Copyright © 2000 Society of Automotive Engineers, Inc.
1999
- Numerical analysis of the influence of the stroke to bore ratio on tumble breakdown
[Relazione in Atti di Convegno]
Bianchi, GIAN MARCO; Cantore, Giuseppe; D., Nicolini; L., Sassi; L., Fraboni
abstract
n.d.