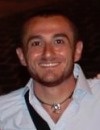 |
GIUSEPPE CICALESE
COLLABORATORE DI RICERCA Dipartimento di Ingegneria "Enzo Ferrari"
|
Home |
Pubblicazioni
2023
- Refined Structural Design and Thermal Analyses of a High-Speed Wound-Field Generator for the More Electrical Aircraft
[Relazione in Atti di Convegno]
Guiducci, A.; Barbieri, S. G.; Nuzzo, S.; Barater, D.; Berni, F.; Cicalese, G.; Fontanesi, S.; Franceschini, G.
abstract
2021
- Computational Fluid Dynamics (CFD) Analysis of Lubricant Oil Tank Sloshing of a High-Performance Car under Racetrack Maneuvers
[Articolo su rivista]
Fontanesi, S.; Olcuire, M.; Cicalese, G.; Lamberti, L.; Pulvirenti, F.; Berni, F.
abstract
The paper proposes a methodology to perform sloshing analyses through multidimensional Computational Fluid Dynamics (CFD), with particular focus on a lubricant tank of a high-performance sports car. Lubricant tanks are usually fed by a mixture of oil and air, which makes Volume of Fluid (VoF) models unsuitable for this kind of simulation. Hence, a different approach based on a Eulerian MultiPhase (EMP) model is investigated and adopted. In contrast to the VoF approach, which is the most consolidated technique to handle the numerical analysis of sloshing problems, the EMP accounts for interactions between liquid and gaseous phases, such as mixing and separation. It also reduces numerical constraints on time-step and mesh size. EMP is therefore applied to the analysis of a sports car lubricant tank where mist and foam formation and subsequent phase separation are of primary importance. Comparison between the EMP and VoF approach is performed on cases of increasing complexity. Firstly, a rectangular tank with internal baffles and under pitch oscillations, for which experimental measurements are available, is analyzed. The EMP approach shows improved responsiveness in representing both phase mixing and separation. Secondly, a current production lubricant oil tank, for which experimental test-rig measurements of foam percentage shortly upstream the feeding pump are available, confirms the ability of the EMP approach to quantitatively estimate foam formation. Thirdly, the analysis of a current production lubricant oil tank subject to typical racetrack maneuvers is performed. Such final step confirms the ability of the EMP approach to simulate complex interactions between the phases, which largely affect tank and lubricating circuit performance in high-performance sports car applications. Moreover, the EMP approach allows a massive reduction of computational time compared to VoF.
2021
- Towards grid-independent 3D-CFD wall-function-based heat transfer models for complex industrial flows with focus on in-cylinder simulations
[Articolo su rivista]
Berni, F.; Cicalese, G.; Borghi, M.; Fontanesi, S.
abstract
Convective heat transfer heavily affects both efficiency and reliability in many industrial problems. For this reason, its proper estimation is mandatory since the early design stage. 3D-CFD simulations represent a powerful tool for the prediction of the heat fluxes. This is even more true considering that typical operating conditions of many applications prevent experimental characterization. As for 3D-CFD computations, the combination of Reynolds Averaged Navier Stokes (RANS) turbulence modeling and high-Reynolds wall treatment is still widely diffused in the industrial practice, to save both computational cost and time. The adoption of a high-Reynolds wall treatment based on wall functions, which permits the use of relatively coarse near-wall grids, implies specific restrictions for the height of the near-wall cell layer. In particular, the first cell-centroid must be placed in the fully turbulent (log-) region of the boundary layer. The main drawback of a cell-centroid falling into the viscous sub-layer consists in a huge overestimation of both wall shear stress and wall heat transfer. The lower the y+ is (i.e. the lower the wall distance is), the higher the predicted values are. As for many other industrial applications, Internal Combustion Engine (ICE) in-cylinder simulations remarkably suffer from the presence of low y+ values in the computational domain, mostly at part-loads and low-revving speeds. At specific operating points, such as idle conditions, it is nearly impossible to maintain y+ in the log-region, even during the compression stroke, when the velocity field should allow the dimensionless distance to reach the highest values in the engine cycle. To avoid such undesired overestimations of shear stress and heat transfer, a modified formulation of the thermal law of the wall (T+) to be used in the viscous sub-layer is proposed in the present paper. To further reduce the grid-dependency of the high-Reynolds wall treatment, a similar modification is applied to the velocity wall function (u+). Resulting wall heat flux and wall shear stress are shown to be grid-independent, at least for y+>3. The proposed alternative modeling for u+ inside the viscous sub-layer is validated in terms of flow field against experimental Laser-Doppler Anemometry (LDA) data and Direct Numerical Simulation (DNS) results. Despite the present analysis focuses on in-cylinder simulations, the alternative u+ and T+ formulations can be applied to any complex flow. Furthermore, the proposed modified laws of the wall can be adopted in conjunction with any wall-function-based heat transfer model.
2019
- A comparison between different moving grid techniques for the analysis of the TCC engine under motored conditions
[Relazione in Atti di Convegno]
Barbato, Alessio; Rulli, Federico; Fontanesi, Stefano; D'Adamo, Alessandro; Berni, Fabio; Cicalese, Giuseppe; Perrone, Antonella
abstract
The accurate representation of Internal Combustion Engine (ICE) flows via CFD is an extremely complex task: it strongly depends on a combination of highly impacting factors, such as grid resolution (both local and global), choice of the turbulence model, numeric schemes and mesh motion technique. A well-founded choice must be made in order to avoid excessive computational cost and numerical difficulties arising from the combination of fine computational grids, high-order numeric schemes and geometrical complexity typical of ICEs. The paper focuses on the comparison between different mesh motion technologies, namely layer addition and removal, morphing/remapping and overset grids. Different grid strategies for a chosen mesh motion technology are also discussed. The performance of each mesh technology and grid strategy is evaluated in terms of accuracy and computational efficiency (stability, scalability, robustness). In particular, a detailed comparison is presented against detailed PIV flow measurements of the well-known "TCC Engine III" (Transparent Combustion Chamber Engine III) available at the University of Michigan. Since many research groups are simultaneously working on the TCC engine using different CFD codes and meshing approaches, such engine constitutes a perfect playground for scientific cooperation between High-Level Institutions. A motored engine condition is chosen and the flow evolution throughout the engine cycle is evaluated on four different section planes. Pros and cons of each grid strategy as well as mesh motion technique are highlighted and motivated.
2019
- On the existence of universal wall functions in in-cylinder simulations using a low-Reynolds RANS turbulence model
[Relazione in Atti di Convegno]
Berni, F.; Cicalese, G.; Sparacino, S.; Cantore, G.
abstract
Heat Transfer plays a fundamental role in internal combustion engines, as able to affect several aspects, such as efficiency, emissions and reliability. As for this last, a proper heat transfer prediction is mandatory for the estimation of the engine temperatures at peak power condition, it being the most critical one from a thermal point of view. At part-load/low revving speed operations, heat transfer is detrimental for the engine efficiency, deeply reducing indicated work of the burnt gases on the piston. Focusing on the in-cylinder domain, 3D-CFD simulations represent an irreplaceable tool for the estimation of gas-to-wall heat fluxes. Several models have been developed in the past, aiming at providing a reliable estimation of the heat transfer at any condition in terms of load and revving speed. To save computational cost and time, the most diffused wall approach for the numerical simulation of confined reacting flows is the high-Reynolds one, which means that heat transfer model is based on a thermal wall function. Unfortunately, wall functions (logarithmic profiles of the inertial layer) can be claimed only at restricted conditions, such as isothermal steady-state flow, velocity parallel to the wall and negligible pressure gradient. In practice, none of these assumptions is valid for industrial applications such as an in-cylinder simulation. Therefore in these cases, as demonstrated by different works in the past, wall functions do not exist and their adoption leads to a non-negligible error in the estimation of the heat transfer. The main goal of this work is to build up a methodology able to investigate the presence of wall functions in actual industrial applications, in particular in 3D-CFD in-cylinder analyses. Compared to previous works available in literature, where DNS or LES are carried out on simplified geometries and/or at low revving speed conditions because of the computational cost, in the present paper a RANS approach to turbulence and a low-Reynolds wall treatment are adopted. Moreover, a new strategy to obtain dimensionless profiles of velocity and temperature from computed fields is introduced. At first, the proposed methodology is validated on a 2D plane channel. Then, a preliminary application on a research engine, namely the GM Pancake engine, is proposed, showing that dimensionless profiles of velocity and temperature calculated on the combustion chamber walls are remarkably different from standard analytical wall functions.
2017
- A Comprehensive CFD-CHT Methodology for the Characterization of a Diesel Engine: From the Heat Transfer Prediction to the Thermal Field Evaluation
[Relazione in Atti di Convegno]
Cicalese, Giuseppe; Berni, Fabio; Fontanesi, Stefano; D'Adamo, Alessandro; Andreoli, Enrico
abstract
High power-density Diesel engines are characterized by remarkable thermo-mechanical loads. Therefore, compared to spark ignition engines, designers are forced to increase component strength in order to avoid failures. 3D-CFD simulations represent a powerful tool for the evaluation of the engine thermal field and may be used by designers, along with FE analyses, to ensure thermo-mechanical reliability. The present work aims at providing an integrated in-cylinder/CHT methodology for the estimation of a Diesel engine thermal field. On one hand, in-cylinder simulations are fundamental to evaluate not only the integral amount of heat transfer to the combustion chamber walls, but also its point-wise distribution. To this specific aim, an improved heat transfer model based on a modified thermal wall function is adopted to estimate correctly wall heat fluxes due to combustion. On the other hand, a detailed Conjugate Heat Transfer model including both the solid components and the coolant circuit of the engine is needed, accounting for all the thermo-mechanical effects acting simultaneously during actual operations. Such comprehensive CHT methodology is here presented, with particular emphasis on a dedicated framework for the thermal simulation of the piston, to account for the mutual influence of many interplaying phenomena such as oil jet impingement, frictional losses and conduction with the surrounding components. The predictive capabilities of the methodology are demonstrated both in terms of global thermal balance and local engine temperature distribution. In fact, numerical coolant heat rejection and thermal field are compared with experimental data provided by thermal survey and point-wise temperature measurements for two different mid-to-low revving speed operating conditions.
2017
- A modified thermal wall function for the estimation of gas-to-wall heat fluxes in CFD in-cylinder simulations of high performance spark-ignition engines
[Articolo su rivista]
Berni, Fabio; Cicalese, Giuseppe; Fontanesi, Stefano
abstract
Last generation spark ignition (SI) engines are characterized by a simultaneous reduction of the engine displacement and an increase of the brake power; such conflicting targets are achieved through the adoption of several techniques such as turbocharging, direct fuel injection, variable valve timing and variable port lengths. This design approach, referred to as “engine downsizing”, leads to a remarkable increase in the thermal loads acting on the engine components facing the combustion chamber. Hence, an accurate evaluation of the thermal field is of primary importance in order to avoid thermo-mechanical failures. Moreover, the correct evaluation of the temperature distribution improves the prediction of point-wise abnormal combustion onset. Due to the complexity of the experimental measurement of instantaneous gas-to-wall heat fluxes, 3D-CFD simulations of the in-cylinder processes are a fundamental tool to evaluate not only the global amount of heat transferred to the combustion chamber walls, but also its point-wise distribution. Several heat transfer models and thermal laws of the wall are available in literature, most of which were developed in the past decades and calibrated against experiments carried out in research laboratories at relatively low-load/low-speed engine operations. In the present paper two widely adopted heat transfer models are proved to be effective at such conditions to predict gas-to-wall heat flux, as demonstrated by their application to the well-known GM pancake engine test case. However, despite such comforting results, they manifest evident shortages when used for highly-charged/highly-downsized current production SI engines, since operated at specific thermal loads and engine speeds very different from the above experiments. In particular, overestimations of the wall heat transfer predicted by such thermal laws of the wall are pointed out thanks to experimental engine thermal surveys and temperature measurements on four current production engines. Therefore an alternative heat transfer model is proposed by the authors and tested on such currently made turbocharged SI engines, operated at different conditions. Compared to the existing models differences are pointed out, especially in terms of law of the wall expression. Experimental engine thermal survey and point-wise temperature measurements are used to validate the numerical heat flux. In particular the increased predictive capabilities of the 3D-CFD gas-to-wall heat transfer simulations are revealed both in terms of global thermal balance and temperature distribution of the metal for all the investigated engines. In fact model adoption in a combined in-cylinder/CHT (Conjugate Heat Transfer) simulation loop leads to a correct characterization of the thermal status of all the analyzed engines. Finally, alternative model adoption for the investigated current production high specific power DISI turbocharged engines operated at full load and high revving speed is critically motivated adopting the “isothermicity parameter” ζ which represents an indication of the thermal state of the boundary layer, being a characteristic scale of the ratio between gas and wall temperatures.
2017
- Critical aspects on the use of thermal wall functions in CFD in-cylinder simulations of spark-ignition engines
[Articolo su rivista]
Berni, Fabio; Fontanesi, Stefano; Cicalese, Giuseppe; D'Adamo, Alessandro
abstract
CFD and FE tools are intensively adopted by engine manufacturers in order to prevent thermo-mechanical failures reducing time and cost-to market. The capability to predict correctly the physical factors leading to damages is hence essential for their application in the industrial practice. This is even more important for last generation SI engines, where the more and more stringent need to lower fuel consumption and pollutant emissions is pushing designers to reduce engine displacement in favor of higher specific power, usually obtained by means of turbocharging. This brings to a new generation of SI engines characterized by higher and higher adiabatic efficiency and thermo-mechanical loads. A recent research highlighted the different behavior of the thermal boundary layer of such engines operated at high revving speeds and high loads if compared to the same engines operated at low loads and revving speeds or even engines with a lower specific power. This means that CFD heat transfer models proposed and validated in the past decades on these last may not be predictive when applied to high specific power engines. This is why an alternative formulation was proposed in a previous work, for the estimation of the heat transfer in in-cylinder CFD simulations of high performance turbocharged SI engines. Nevertheless, for both the proposed alternative thermal wall function and the other ones available in literature, there are essential limitations due to the dimensionless distance y+. In fact, even if heat transfer models provide a further formulation for low y+ (viscous sub-layer), industrial practice seldom makes use of turbulence models enabling the integration up to the wall and low Reynolds approaches are even less used because of computational costs. Therefore in the present paper the authors aim to analyze critically the use of thermal wall functions along with high Reynolds turbulence models for the prediction of heat transfer in CFD in-cylinder simulations for different values of y+.
2016
- Integrated In-Cylinder / CHT Methodology for the Simulation of the Engine Thermal Field: An Application to High Performance Turbocharged DISI Engines
[Articolo su rivista]
Cicalese, Giuseppe; Berni, Fabio; Fontanesi, Stefano
abstract
New SI engine generations are characterized by a simultaneous reduction of the engine displacement and an increase of the brake power; such targets are achieved through the adoption of several techniques such as turbocharging, direct fuel injection, variable valve timing and variable port lengths. This design approach, called "downsizing", leads to a marked increase in the thermal loads acting on the engine components, in particular on those facing the combustion chamber. Hence, an accurate evaluation of the thermal field is of primary importance in order to avoid mechanical failures. Moreover, the correct evaluation of the temperature distribution improves the prediction of pointwise abnormal combustion onset. The paper proposes an evolution of the CFD methodology previously developed by the authors for the prediction of the engine thermal field, which is applied to two different high performance turbocharged DISI engines: the methodology employs both in-cylinder 3D-CFD combustion simulations and CHT (Conjugate Heat Transfer) simulations of the whole engine, inclusive of both the solid components and the coolant circuit. In-cylinder analyses are used as thermal boundary conditions for the CHT simulations, which are in turn a fundamental benchmark to evaluate the accuracy of the combustion heat flux estimation by means of a combination of global engine thermal survey and local temperature measurements. A preliminary evaluation of some consolidated heat transfer models is carried out to evaluate the accuracy of the predicted gas-to-wall heat fluxes. Then, a modified heat transfer model is proposed, critically motivated and applied to the specific engine conditions under investigations. The proposed model strongly improves the predictive capability of the combined in-cylinder/CHT methodology in terms of both global thermal balance and pointwise temperature distribution for both the investigated engines
2015
- A methodology for the reduction of numerical diffusion in sloshing analyses through automated mesh adaptation
[Relazione in Atti di Convegno]
Fontanesi, Stefano; Cicalese, Giuseppe; De Pasquale, Gianluca
abstract
The paper proposes a methodology to improve the accuracy of Volume of Fluid (VoF) multiphase problems involving liquid/gas sloshing in fuel/lubricant tanks without penalizing the computational cost of the simulations. In order to correctly track the complex trajectory of the liquid/gas interface and the presence of liquid droplets in the gas phase, the VoF method requires a fine mesh at each interface location to reduce modeling errors. The investigated case is a lubricant tank of a sport car subject to typical race track maneuvers. Due to the geometrical extent and the complexity of the computational domain and to the relevant accelerations, resulting in dispersed liquid structures within the gas phase, the use of a generalized fine mesh would result in computational costs far beyond the industrial practice. A methodology is then proposed to reduce the overall number of computational cells through a combination of local interface tracking and mesh refinement, which is combined with an active control of the time step to comply with Courant-Friedrichs- Lewy number limits. The methodology is at first validated against experimental measurements for a simplified test case, and then applied to the actual oil tank sloshing case, showing a relevant reduction of the numerical diffusion and a consequent higher accuracy.
2015
- Effects of Fuel-Induced Piston-Cooling and Fuel Formulation on the Formation of Fuel Deposits and Mixture Stratification in a GDI Engine
[Relazione in Atti di Convegno]
Giovannoni, Nicola; D'Adamo, Alessandro; Cicalese, Giuseppe; Cantore, Giuseppe
abstract
Fuel deposits in DISI engines promote unburnt hydrocarbon and soot formation: due to the increasingly stringent emission regulations (EU6 and forthcoming), it is necessary to deeply analyze and well-understand the complex physical mechanisms promoting fuel deposit formation. The task is not trivial, due to the coexistence of mutually interacting factors, such as complex moving geometries, influencing both impact angle and velocity, and time-dependent wall temperatures. The experimental characterization of actual engine conditions on transparent combustion chambers is limited to highly specialized research laboratories; therefore, 3D-CFD simulations can be a fundamental tool to investigate and understand the complex interplay of all the mentioned factors. The aim is pursued in this study by means of full-cycle simulations accounting for instantaneous fuel/piston thermal interaction and actual fuel characteristics. To overcome the standard practice, based on the adoption of time-independent wall temperatures, solid cell layers are added onto the piston crown. In particular, thermal boundary conditions on the lower face of the piston portion are derived from a complete CHT simulation, thus considering both the actual piston shape and the point-wise cooling effect by the oil jets, the friction contribution and the heat transfer to the cylinder liner and the connecting rod. Furthermore, the use of a simplified fuel model based on a single-component formulation is compared to a more realistic hydrocarbon blend. The methodology is applied to a currently produced turbocharged DISI engine operating at full load peak power and maximum torque regimes; the piston thermal field is completely resolved in space and time during the engine cycle, and its effects on spray guidance, fuel impingement and liquid film formation are carefully analyzed.
2014
- A Methodology to Improve Knock Tendency Prediction in High Performance Engines
[Relazione in Atti di Convegno]
Fontanesi, Stefano; Cicalese, Giuseppe; D'Adamo, Alessandro; Cantore, Giuseppe
abstract
The paper presents a comprehensive numerical methodology for the estimation of knock tendency in SI engines, based on the synergic use of different frameworks [1]. 3D-CFD in-cylinder analyses are used to simulate the combustion and to estimate the
point-wise heat flux acting on engine components. The resulting heat fluxes are used in a conjugate heat transfer model in order to reconstruct the actual point-wise wall temperature distribution. An iterative loop is established between the two simulation realms. In order to evaluate the effect of temperature on knock, in-cylinder analyses are integrated with an accurate chemical description of the actual fuel.
2014
- Integrated In-Cylinder/CHT Analysis for the Prediction of Abnormal Combustion Occurrence in Gasoline Engines
[Relazione in Atti di Convegno]
Fontanesi, Stefano; Cicalese, Giuseppe; Cantore, Giuseppe; D'Adamo, Alessandro
abstract
In order to improve fuel conversion efficiency, currently made spark-ignited engines are characterized by the adoption of gasoline direct injection, supercharging and/or turbocharging, complex variable valve actuation strategies. The resulting increase in power/size ratios is responsible for substantially higher average thermal loads on the engine components, which in turn result in increased risks of both thermo-mechanical failures and abnormal combustion events such as surface ignition or knock. The paper presents a comprehensive numerical methodology for the accurate estimation of knock tendency of SI engines, based on the integration of different modeling frameworks and tools. Full-cycle in-cylinder analyses are used to estimate the point-wise heat flux acting on the engine components facing the combustion chamber. The resulting cycle-averaged heat fluxes are then used in a conjugate heat transfer model of the whole engine in order to reconstruct the actual point-wise temperature distribution of the combustion chamber walls. The two simulation realms iteratively exchange information until convergence is met. Particularly, the effect of point-wise temperature distribution on the onset of abnormal combustion events is evaluated. In-cylinder analyses account for the actual autoignition behavior of the air/fuel mixture through a look-up table approach: the combustion chamber is treated as a two-zone region (burnt/unburnt), where ignition delay tabulation, generated off-line using a constant pressure reactor, is applied to the unburnt region to estimate cell-wise knock proximity. The methodology is applied to a high performance engine and the importance of an accurate representation of the combustion chamber thermal boundary conditions when aiming at precisely evaluating the surface ignition/knock tendency is highlighted.
2014
- Numerical investigation of the cavitation damage in the wet cylinder liner of a high performance motorbike engine
[Articolo su rivista]
Fontanesi, Stefano; Giacopini, Matteo; Cicalese, Giuseppe; Sissa, Simone; S., Fantoni
abstract
In this paper a numerical methodology is proposed which aims at understanding the origin of a particular failure occurred in a two-cylinder high performance spark ignition engine for motorbike applications. A relevant cavitation damage/erosion has been detected at the water side of the engine cylinder liner during severe reliability bench tests, performed at the early stage of the engine design process. On the contrary, no damages have been registered during parallel high-load long runs of the motorbike. This contribution investigates in detail the differences between the bench test cooling circuit layout and the actual motorbike cooling circuit layout in order to find an explanation of the engine critical behaviour. In particular, CFD-CHT analyses of the water cooling jacket are performed, the computational domain covering both the coolant galleries and the surrounding metal components (head, block, gasket, valves, valve seats, valve guides, cylinder liner, spark plug). The contribution of a two-phase approach which takes into account the effect of a phase transition within the engine coolant is considered. Different engine operating conditions are investigated and a detailed analysis of different thermo-mechanical parameters influencing the engine behaviour is carried out. Results of the CFD simulations asses the methodology capability to correctly capture and understand the origin of the engine failure, thus providing a useful design tool for a faster and more effective design modification.
2013
- Analysis of Turbulence Model Effect on the Characterization of the In-Cylinder Flow Field in a HSDI Diesel Engine
[Relazione in Atti di Convegno]
Fontanesi, Stefano; Cicalese, Giuseppe; Severi, Elena
abstract
In-cylinder large scale and small scale structures are widely recognized to strongly influence the mixing process in HSDI Diesel engines, and therefore combustion and pollutant emissions. In particular, swirl motion intensity and temporal evolution during the intake and compression strokes must be correctly estimated to properly target the spray jets. The experimental characterization of the attitude of a valve/port assembly to promote swirl is traditionally limited to the steady flow bench, in which the analysis is carried out for fixed valve positions / fixed pressure drops and with no piston. Since flow bench analyses cannot reproduce the highly complex instantaneous flow conditions typical of actual engine operations, the use of fully-transient in-cylinder numerical simulations can become extremely useful to correctly address the engine ability to promote adequate flow structures and patterns.
CFD analyses of in-cylinder flow motion development and decay are usually carried out using relatively simple yet stable turbulence models, among which k-epsilon and RNG k-epsilon, in conjunction with near-wall algebraic functions, are probably the most popular ones. Nevertheless, it is widely recognized that such models show deficiencies in correctly capturing complex rotating flow structures such as those dominating in-cylinder flows of compression ignition engines. While waiting for the diffusion of more refined approaches such as Large Eddy Simulation (LES) or Detached Eddy Simulation (DES), the use of better performing RANS models such as Reynolds Stress and k-omega SST, in conjunction with adequate resolution of the near wall flow, would be recommendable.
The paper reports a numerical activity aiming at evaluating the influence of the turbulence model choice on the prediction of in-cylinder flow patterns in a HSDI Diesel engine for automotive applications. Three different engine operations are investigated, i.e. two part-load / low engine speeds ones and a full-load / peak power engine speed one. For each engine condition, both wall-function k-epsilon and low-Reynolds k-omega SST models are used, and for the last one two different near-wall grid refinements are adopted. In order to better assess the predictive capabilities of the models, analyses are preliminarily compared to experimental measurements for both a simplified engine-like geometry and flow structure available in literature and steady flow-bench operations of the actual engine head.
2013
- Combined In-cylinder / CHT Analyses for the Accurate Estimation of the Thermal Flow Field of a High Performance Engine for Sport Car Applications
[Relazione in Atti di Convegno]
Fontanesi, Stefano; Cicalese, Giuseppe; A., Tiberi
abstract
The paper describes an integrated methodology for the accurate characterization of the thermal behavior of internal combustion engines, with particular reference to a high performance direct injected SI engine for sport car applications. The engine is operated at full load and maximum power revving speed, which is known to be critical from the point of view of thermal stresses on the engine components.
In particular, two different sets of 3D-CFD calculations are adopted: on one side, full-cycle in-cylinder analyses are carried out to estimate the point wise thermal heat flux due to combustion on the engine components facing the combustion chamber. On the other side, full-engine multi-region CHT calculations covering the engine coolant jacket and the surrounding metal components are used to compute the point wise temperature distribution within the engine head, liner and block.
An iterative procedure is then implemented in order to exchange relevant thermal data between the two modeling frameworks: at first, local gas temperatures and heat transfer coefficients from the in-cylinder simulations are applied as thermal loads to the CHT calculations; then, the resulting surface temperature maps are re-applied to the combustion chamber walls for the subsequent in-cylinder CFD analysis. The procedure is iteratively repeated until convergence is met in terms of thermal characterization of the engine.
The procedure takes into account the non-uniform spatial distribution of both thermal loads from the combustion process and resulting temperature distribution on the combustion chamber walls, which are known to be particularly evident when considering direct injected stratified charged engines. The resulting thermal fields are compared to those deriving from a traditional approach for both the in-cylinder and CHT calculations, i.e. the application of uniform heat fluxes on the CHT side and the use of uniform wall temperatures on the in-cylinder side. The resulting differences are highlighted and critically discussed, with particular emphasis on those which could have a relevant impact on both the fatigue strength evaluation of the engine and the arising of local undesired phenomena such as surface ignition and knocking.
2011
- CFD Investigation of the Thermo-Mechanical Behavior of a High Performance Bike Engine
[Relazione in Atti di Convegno]
Fontanesi, Stefano; Cicalese, Giuseppe; S., Fantoni; M., Rosso
abstract
The paper presents a combined experimental and numerical activity carried out to improve the accuracy of conjugate heat transfer CFD simulations of a high-performance S.I. motorbike engine water cooling jacket. The computational domain covers both the coolant jacket and the surrounding metal components (head, block, gasket, valves, valve seats, valve guides, cylinder liner, spark plug).In view of the complexity of the modeled geometry, particular care is required in order to find a tradeoff between the accuracy and the cost-effectiveness of the numerical procedure. The CFD-CHT simulation of water cooling jackets involves many complex physical phenomena: in order to setup a robust numerical procedure, the contribution of some relevant CFD parameters and sub-models was discussed by the authors in previous publications and is referred to [1-4].Among the formers, the effects of a proper set of boundary conditions and a detailed representation of the physical properties of the involved materials were evaluated. Among the latter, the contribution of a two-phase approach taking into account the effects of phase transition within the engine coolant was considered.The CFD-CHT setup is now applied to investigate and understand the origin of a critical engine behavior occurring at the engine test bench under a severe reliability test. Additional sub-models are introduced and their impact on the results is discussed. Different engine operations are modeled and a detailed analysis of the many thermo-mechanical factors influencing the engine fatigue strength is carried out.At the end of the process, CFD simulations are able to correctly capture and understand the origin of the engine failure, thus leading to a faster and more effective design modification.
2011
- Validation of a CFD Methodology for the Analysis of Conjugate Heat Transfer in a High Performance SI Engine
[Relazione in Atti di Convegno]
Fontanesi, Stefano; Cicalese, Giuseppe; D'Adamo, Alessandro; G., Pivetti
abstract
The paper presents a combined experimental and numerical activity carried out to improve the accuracy of conjugate heat transfer CFD simulations of a high-performance S.I. engine water cooling jacket.Due to the complexity of the computational domain, which covers both the coolant jacket and the surrounding metal cast (both head and block), particular care is required in order to find a tradeoff between the accuracy and the cost-effectiveness of the numerical procedure. In view of the presence of many complex physical phenomena, the contribution of some relevant CFD parameters and sub-models is separately evaluated and discussed.Among the formers, the extent of the computational domain, the choice of a proper set of boundary conditions and the detailed representation of the physical properties of the involved materials are separately considered. Among the latters, the choice between a simplified single-phase approach and a more complex two-phase approach taking into account the effects of phase transition within the engine coolant is discussed.The predictive capability of the CFD-CHT methodology is assessed by means of the comparison between CFD results and experimental measurements provided by the engine manufacturer for different engine operating conditions.At the end of the validation process, a methodology for the correct and cost-effective characterization of conjugate heat transfer is proposed, showing a reasonable trade-off between the predictive capability and the computational effort of the simulations.
2010
- Analisi Termo-Meccanica a Fatica di un Motore Diesel Automobilistico
[Relazione in Atti di Convegno]
Cantore, Giuseppe; Fontanesi, Stefano; Cicalese, Giuseppe; Strozzi, Antonio; Giacopini, Matteo
abstract
L’articolo presenta alcuni risultati relativi all’analisi termo-meccanica di un motore Diesel automobilistico. Lo studio è condotto utilizzando simulazioni disaccoppiate CFD e FEM allo scopo di valutare la resistenza a fatica del motore. Una metodologia semplificata per stimare la caratteristica termo-meccanica di testate motore soggette alle reali condizioni operative è stata proposta dagli autori in precedenti pubblicazioni [1,2], ed è ora affinata apportando rilevanti miglioramenti su entrambi i fronti di simulazione.Dal lato CFD, l’analisi CHT (conjugate heat transfer) include nel dominio di calcolo anche il metallo del basamento, dei componenti forzati della testa, nonché della guarnizione. Particolare cura è rivolta alla rappresentazione dello strato limite e all’applicazione delle condizioni al contorno termiche, in particolare alla distribuzione dei flussi termici tra i vari componenti motore. Al fine di massimizzare l’accuratezza delle previsioni CFD, sono valutati criticamente gli effetti dell’ebollizione del refrigerante sulla previsione dello scambio termico.L’accuratezza della previsione numerica viene valutata mediante confronto con misure sperimentali di temperatura in alcuni punti della testa per condizioni stazionarie di funzionamento del motore. I risultati delle simulazioni CFD, ed in particolare la distribuzione puntuale del flusso di calore all’interfaccia fluido/solido, sono trasferiti come condizione al contorno all’analisi termo-strutturale tramite una routine appositamente realizzata. Dal lato termo-meccanico, la principale novità introdotta è l’implementazione di un criterio di tipo energetico per la stima della resistenza a fatica a basso numero di cicli; tale criterio, utilizzato congiuntamente ai più classici criteri tensionali o deformativi, consente di disporre di uno strumento di progettazione capace di predire la resistenza delle singole parti del motore soggette ai differenti carichi agenti. Sono infatti analizzati carichi affaticanti sia ad alto sia a basso numero di cicli, e la metodologia proposta è applicata con successo per predire i possibili punti di innesco di fratture sulla testa e migliorare le caratteristiche del circuito di raffreddamento.
2010
- Multiphase CFD-CHT Analysis and Optimization of the Cooling Jacket in a V6 Diesel Engine
[Relazione in Atti di Convegno]
Fontanesi, Stefano; Cicalese, Giuseppe; Giacopini, Matteo
abstract
The paper presents a numerical activity directed at the analysis and optimization of internal combustion engine water cooling jackets, with particular emphasis on the fatigue-strength assessment and improvement.In the paper, full 3D-CFD and FEM analyses of conjugate heat transfer and load cycle under actual engine operation of a single bank of a current production V6 turbocharged Diesel engine are reported.A highly detailed model of the engine, made up of both the coolant galleries and the surrounding metal components, i.e. the engine head, the engine block, the gasket, the valve guides and valve seats, is used on both sides of the simulation process to accurately capture the influence of the cooling system layout under thermal and load conditions as close as possible to actual engine operations.Concerning the CFD side, a 50-50 binary mixture of ethylene-glycol and water is used in order to correctly reproduce the coolant behavior, while boundary conditions are derived from a combination of experimental measurements and a CFD-1D model of the whole engine.In order to find a proper CFD setup for the optimization of the thermal behavior of the engine, a preliminary comparison between experimental temperature distribution within the engine head and CFD forecasts is carried out. Eight thermocouples are used to measure the engine head local temperature at some critical locations.Among the many competing numerical sub-models involved in the CFD simulations, particular attention is devoted to the modeling of phase transition and vapor nuclei formation within the coolant galleries.Concerning the FEM side, thermo-mechanical analyses are carried out aiming at addressing the design optimization of the engine in terms of fatigue strength. In view of the wide range of thermal and load conditions, both high-cycle and low-cycle fatigue must be properly characterized by means of ad-hoc criteria. An energy-based criterion specifically suited for low-cycle fatigue regions is therefore superimposed to well-established S-N o ε-N criteria for the high cycle fatigue regions.The proposed methodology shows very promising results in terms of point-wise detection of possible engine failures ans proves to be an effective tool for the accurate thermo-mechanical characterization of internal combustion engines under actual life-cycle operations.
2010
- Sviluppo di un Motore Diesel Due Tempi Veloce per Propulsione Aeronautica
[Relazione in Atti di Convegno]
Cantore, Giuseppe; Mattarelli, Enrico; Fontanesi, Stefano; Paltrinieri, Fabrizio; Rinaldini, Carlo Alberto; Perini, Federico; Malaguti, Simone; Severi, Elena; Cicalese, Giuseppe
abstract
Nel campo della propulsione aeronautica per velivoli leggeri, si è recentemente sollevato un forte interesse verso i motori Diesel a due tempi, allo scopo di sostituire i tradizionali motori ad accensione comandata, per i quali risulterà sempre più difficile il reperimento del carburante “avio” negli aeroporti. L’obbiettivo di questo studio è dunque quello di individuare e confrontare tra loro possibili configurazioni adatte all’applicazione aereonautica. Il propulsore scelto come riferimento è prodotto dall’azienda australiana WAM, ha una potenza di 100/120 HP, ed è dotato di sovralimentazione a due stadi, iniezione indiretta, lavaggio unidirezionale (con valvole di scarico in testa).Il primo “step” evolutivo che si è studiato è la trasformazione ad iniezione diretta, con camera a tazza ricavata nel pistone ed iniettore di tipo Common Rail: questa modifica offre il vantaggio di un notevole incremento di potenza ed efficienza, abbinata ad una riduzione delle masse radianti. Oltre a ciò, si è anche analizzato a calcolo un sistema di combustione innovativo, basato su un lavaggio ad anello, senza ausilio di valvole. A fronte della notevole compattazione del motore, aspetto assai apprezzabile in campo aeronautico, con questa soluzione risulta però più difficile ottimizzare lavaggio e combustione, mancando completamente il riferimento a motori moderni.Partendo dal motore base, è stato anzitutto costruito e calibrato sperimentalmente un modello di simulazione termo-fluidodinamico monodimensionale. In parallelo sono state svolte anche simulazioni CFD-3D utilizzando STAR-CD per l’analisi del lavaggio, e KIVA-3V per lo studio della combustione. Queste analisi di dettaglio hanno consentito di caratterizzare i principali processi termo-fluidodinamici che avvengono nelle diverse configurazioni alternative, che sono poi state poste a confronto tramite analisi di ciclo.
2010
- Sviluppo di una metodologia CFD e FEM per l’analisi a fatica di componenti motoristici
[Relazione in Atti di Convegno]
Cantore, Giuseppe; Fontanesi, Stefano; Cicalese, Giuseppe; Strozzi, Antonio; Giacopini, Matteo
abstract
L’articolo presenta alcuni risultati relativi all’analisi termo-meccanica di un motore Diesel automobilistico 6 cilindri a V di cilindrata complessiva 2900cc. Lo studio è condotto utilizzando simulazioni disaccoppiate CFD e FEM allo scopo di valutare la resistenza a fatica dei componenti. La distribuzione di fluido nel circuito di raffreddamento è stata in precedenza oggetto di approfondite analisi e ottimizzazioni al fine di migliorare le caratteristiche dei passaggi del refrigerante. Una metodologia semplificata al fine di stimare la caratteristica termo-meccanica di testate motore soggette alle reali condizioni operative è stata proposta dagli autori in precedenti pubblicazioni. Come conseguenza dell’elevata complessità dei vari fenomeni coinvolti, in questo articolo si introducono alcune importanti migliorie, che consentono un’analisi più accurata della resistenza a fatica del motore, soggetto a carichi affaticanti ad alta frequenza e a bassa frequenza. La metodologia oggetto del presente articolo si basa ancora una volta sull’analisi disaccoppiata CFD e FEM, con rilevanti miglioramenti apportati su entrambi i fronti di simulazione. Dal lato CFD, si utilizza una nuova tipologia di griglia poliedrica, che riesce a combinare l’elevata risoluzione spaziale della mesh con una richiesta computazionale accettabile e un’elevata stabilità numerica della simulazione; particolare attenzione viene dedicata alla rappresentazione del flusso in parete. Mediante l’analisi CFD – CHT (conjugate heat transfer) è valutata la distribuzione puntuale del flusso di calore al refrigerante, includendo nel dominio di calcolo anche il metallo del basamento, della testa completa dei componenti forzati, nonché della guarnizione. Al fine di valutare e incrementare l’accuratezza della previsione numerica, sono stati effettuati e vengono mostrati alcuni confronti con misure sperimentali di temperatura in alcuni punti della testa per condizioni stazionarie di funzionamento del motore. Particolare cura è rivolta alla rappresentazione dello strato limite, fluidodinamico e termico. Allo stesso tempo, grande attenzione è data all’applicazione delle condizioni al contorno termiche, in particolare alla distribuzione dei flussi termici tra i vari componenti affacciati alla camera di combustione. Al fine di massimizzare l’accuratezza delle previsioni CFD, sono valutati criticamente gli effetti dell’ebollizione del refrigerante sulla previsione dello scambio termico tra refrigerante e metallo. I risultati delle simulazioni CFD, ed in particolare la distribuzione puntuale del flusso di calore sulla superficie di contatto fluido/solido, sono successivamente trasferiti come condizione al contorno all’analisi termo-strutturale per la valutazione della resistenza a fatica del componente. A tal fine, si utilizza una routine appositamente realizzata, in grado di mappare la distribuzione puntuale dei flussi termici calcolata tramite le simulazioni CFD su una griglia di calcolo ottimizzata per le analisi FEM. Dal lato termo-meccanico, la principale novità introdotta è l’implementazione di un criterio di tipo energetico per la stima della resistenza a fatica a basso numero di cicli; tale criterio, utilizzato in congiunzione con i più classici criteri tensionali o deformativi, consente di disporre di uno strumento di progettazione capace di predire la resistenza delle singole parti del motore soggette ai differenti carichi agenti. Sono infatti analizzati carichi affaticanti sia ad alto sia a basso numero di cicli, e la metodologia proposta è applicata con successo al fine di predire i possibili punti di innesco di fratture sulla testa e di migliorare le caratteristiche del circuito di raffreddamento.