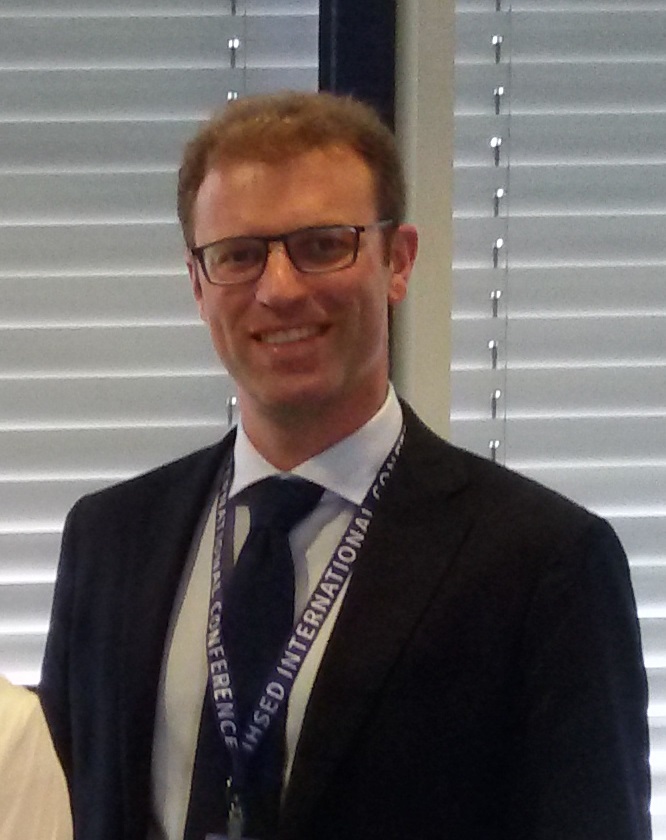 |
ALBERTO VERGNANO
Professore Associato Dipartimento di Ingegneria "Enzo Ferrari"
|
Home |
Curriculum(pdf) |
Didattica |
Pubblicazioni
2024
- Computer-based Design and Manufacturing for the Reproduction of Classic Car Spare Parts
[Relazione in Atti di Convegno]
Bertoncelli, P.; Gherardini, F.; Dalpadulo, E.; Lorient, A.; Vergnano, A.; Leali, F.
abstract
2023
- Simulation-Based Design of Reconfigurable Moulds for Injection Overmoulding
[Relazione in Atti di Convegno]
Galati, N.; Gherardini, F.; Guaitoli, C.; Vergnano, A.
abstract
The injection moulding process enables the production of complex shaped parts, thanks to the accurate kinematics and the tight tolerances of the mould. This process is suitable for large batch production, leading to reduced single part costs, but involves high initial investments. The life of a mould can be increased by exploiting reconfigurable cavity inserts. So, a design method has been conceived for reconfigurable injection moulds by integrating Design for Assembly and Computer Aided Engineering techniques. From the early phases of a systematic design approach, the simulation models are configured with the different geometries as requested by design specifications. The mould inserts are designed with standard features in order to be quickly changed. A case study on a reconfigurable mould for the overmoulding of polymer wheels to be produced in different sizes is presented. The simulations with Moldex3D software are finally compared with the experimental data from the actual production.
2022
- A method for yield and cycle time improvements in Al alloy casting with enhanced conductivity steel for die construction
[Articolo su rivista]
Vergnano, A.; Salvati, E.; Magistrelli, A.; Brambilla, E.; Veronesi, P.; Leali, F.
abstract
A die for Al alloy casting must be designed to achieve the expected quality levels. Moreover, the casting unit cost must be regarded as the objective function to be minimised It can be expressed as a function of the quantity of materials and energy to be used, cycle time and equipment investment. This work compares the performance of the die with inserts manufactured using the usual 1.2343 steel with that of the innovative 1.2383. The latter is considered due to its enhanced thermal conductivity, despite being more expensive. Simulation experiments are designed to evaluate different die layouts. The quality design solutions are evaluated against the cost objective function in order to identify the optimal die choice. A case study on gravity die casting (GDC) of an AlSi7Mg0.3 engine head shows faster solidification dynamics when using 1.2383 instead of 1.2343 steel. This reduces the feeder volume, thus increasing the production yield and speeding up the cycle time with a leverage effect. The higher investment cost for the inserts is rapidly returned thanks to the reduction in variable costs. The Return On Investment (ROI) with the improved die in the new solution is short compared with the life of the die.
2021
- Simulation and experimental validation of Secondary Dendrite Arm Spacing for AlSi7Mg0.3 chassis parts in Low Pressure Die Casting
[Relazione in Atti di Convegno]
Vergnano, Alberto; Bergamini, Umberto; Bianchi, Daniele; Veronesi, Paolo; Spagnolo, Roberto; Leali, Francesco
abstract
The structural properties of cast aluminum parts are strongly affected by the solidification in the production process. The solidification dynamics determines the Secondary Dendrite Arm Spacing (SDAS), directly affecting the structural strength of the alloy. Simulation techniques enable the integrated design of chassis parts and their production equipment. However, in order to effectively predict the SDAS formation, the simulation models need to be investigated and calibrated. The present research investigates the SDAS formation models and identifies a robust relation to be used in Design by Simulation phases for AlSi7Mg0.3 parts.
2021
- Visual motor coordination capabilities of future car drivers in relation to the practised physical activity
[Articolo su rivista]
Vergnano, A.; Tripi, F.; Toni, R.; Calogero, A. L.; Campa, F
abstract
Driving safety is recognized by society as critical for novice car drivers, with specific restrictive measures in road traffic laws and higher insurance premiums. Research has investigated how young people showdeficiencies in the executive function required for driving, due to late brain maturation through adolescence and in early adulthood. Moreover, the modern lifestyle of children and adolescents, with reduced physical activity and the abuse of electronic devices, further decreases their visual motor coordination capabilities, which are fundamental in driving. This research investigates the capabilities of future car drivers in relation to their lifestyle. The experimental method was designed to collect data about the physical activity of students through questionnaires. Thereafter, their visual capabilities were evaluated with a set of field tests, namely Distance Rock, Peripheral Wall Chart and Brock String tests. Finally, their visual motor coordination was assessed with a Motor Efficiency Test. The method was adopted for an extensive study in primary, lower and upper secondary schools, over a large number of tests. The results were evaluated considering age, gender, frequency and type of practised physical activities. The development of visual motor coordination capabilities during child and adolescent growth was assessed. Frequent physical activity improves such coordination. The students practising team sports were found to be more performing, also in terms of visual performance, than the students not practising any sport or those practising individual sports. The data base encourages more extensive studies in the education system, also evaluating the same students over the years.
2020
- A methodology for out of position occupant identification from pressure sensors embedded in a vehicle seat
[Articolo su rivista]
Vergnano, A.; Leali, Francesco
abstract
The airbag deployment against an out of position (OP) occupant is critical. The OP condition can be hardly expected during design, while a too close airbag deployment can cause serious injuries instead of mitigating the crash effects. An adaptive airbag system would be capable to adjust its deployment to the inside scenario. However, the integration between human passengers and intelligent vehicle requires the airbag control unit to be aware of the actual occupant(s) position. In the present research, a methodology for monitoring the occupant(s) position is developed and tested with a seat prototype. A layout of thin film sensors monitors the interface pressure between the occupant and the seat cover. An inertial measurement unit (IMU) monitors the accelerations of the vehicle, considered the reference moving platform. A microcontroller is programmed for pressure sensors calibration, IMU alignment with the vehicle reference system, signals processing, OP detection, and identification. Real driving experiments on a race track were performed in the correct position and in three different OPs. The comparison of the pressure center in longitudinal and transversal directions with the vehicle acceleration enables to identify the OPs.
2020
- A simple test method for measurement of the interface thermal resistance of coated and uncoated metal surfaces
[Relazione in Atti di Convegno]
Pedrazzi, Simone; Vergnano, A.; Allesina, G.; Veronesi, Paolo; Leali, F.; Tartarini, P.; Muscio, A.
abstract
Dies for metal casting must often be coated internally to minimize interaction between the surface of the steel die and the melt metal during pouring and solidification. However, the added coating increases the thermal interface resistance during the cooling process and can thus extend the process duration. For example, numerical predictions and experimental results are matched if the interface resistance is even quintupled in the presence of usual interface coating, compared to the uncoated mold. In order to have a reasonable estimate of the interface thermal resistance, an easy to use measurement approach has been tested. This consists of contacting a cold and a hot samples of metals with known thermal properties, one at ambient temperature and the other one much hotter. The temperatures of the two samples, assumed to be uniform in each sample, are measured by thermocouples, and the interface resistance is retrieved from the time evolution pattern of those temperatures during the thermal transient that follows the instant in which the samples have been contacted.
2020
- Design Tools and Methods in Industrial Engineering, Proceedings of the International Conference on Design Tools and Methods in Industrial Engineering, ADM 2019
[Curatela]
Rizzi, Caterina; Andrisano, Angelo Oreste; Leali, Francesco; Gherardini, Francesco; Pini, Fabio; Vergnano, Alberto
abstract
This book collects the proceedings of the ADM 2019 International Conference, entitled “Design Tools and Methods in Industrial Engineering”, held in Modena, Italy, on 9–10 September 2019. This is not the first time that an event organized by ADM (formerly known as Italian Association of Machines Design, today renamed the Italian Association of Design Methods for Industrial Engineering) or by our scientific sector (ING-IND/15) takes place in Modena. I am pleased to remember the “ADM day” held at the Military Academy of Modena in 2008, as well as the ING-IND/15 workshop organized in 2009 in the hills of Bologna, not far from Modena. However, this conference is particularly significant, for the reasons I wish to summarize here.
Firstly, the ADM Conference constitutes a new international, permanent event held in Italy, aimed at disseminating cutting-edge research to a national and international audience. For several years, our association has had a collaborative relationship with the Spanish members of INGEGRAF and the French members of Smart (formerly AIP-PRIMECA), with whom we organize the International Joint Conference on Mechanics, Design Engineering and Advanced Manufacturing (JCM) every two years. This event is hosted alternately by one of our three countries. Therefore, the ADM International Conference was born from the need for an event “in the middle”, to strengthen the international research network and to meet our colleagues in Italy. As a matter of fact, the ADM 2019 scientific committee was joined by Spanish and French colleagues, as well as German, Swedish, Norwegian and American ones, thanks to partnerships created by our “Enzo Ferrari” Department of Engineering (Modena) over the years.
Secondly, I am honoured to play the role of conference chair, a position that has led me to be one of the editors of this book. In more than 45 years of experience in this sector, I have seen many developments and evolutions. From the first use of CAD in the industrial sector, today we have reached a high multidisciplinary level and integration with information technology and electronics. The integration of novel tools and approaches in the industrial world is also due to the activity of our scientific sector, capable of developing and integrating innovative tools and methodologies with the traditional themes of industrial engineering.
Finally, this conference is held in 2019, an important year for me, marking the conclusion of my mandate as Rector of the University of Modena and Reggio Emilia, as well as that of Full Professor for our scientific sector. As the Dean of the ADM association and the scientific sector, I enthusiastically accepted the proposal of Francesco Leali, my collaborator for years and now my colleague, to nominate the University of Modena and Reggio Emilia, and in particular our “Enzo Ferrari” Department of Engineering, as the location for the ADM 2019 International Conference. I would like to thank both him and my departmental colleagues, in particular the researchers of my lab, LaPIS lab, for organizing this event at the “Enzo Ferrari” Department of Engineering, so dear to me, having been one of its first promoters and founders.
Equally, I would like to thank the ADM President Prof. Vincenzo Nigrelli, and Prof. Caterina Rizzi, Coordinator of the ADM Scientific Council, whose members,
in turn, I gratefully thank. Further thanks go to the publisher, Springer, who honoured us by publishing the proceedings of this first ADM International Conference in the series “Lecture Notes in Mechanical Engineering”. Therefore, as editor of this first book, I hope that it will be the first of a new series of international conference proceedings underlining the leading role of our scientific sector in the international scene. The colleagues who will be hosting the next ADM conferences will have the burden, but above all the honour, of continuing this project that today we have
2020
- Intelligent Human Systems Integration 2020, Proceedings of the 3rd International Conference on Intelligent Human Systems Integration (IHSI 2020): Integrating People and Intelligent Systems
[Curatela]
Ahram, T.; Karwowski, W.; Vergnano, A.; Leali, F.; Taiar, R.
abstract
This volume, entitled Intelligent Human Systems Integration 2020, aims to provide a global forum for introducing and discussing novel approaches, design tools, methodologies, techniques, and solutions for integrating people with intelligent technologies, automation, and artificial cognitive systems in all areas of human endeavor in industry, economy, government, and education. Some of the notable areas of application include, but are not limited to, energy, transportation, urbanization and infrastructure development, digital manufacturing, social development, human health, sustainability, a new generation of service systems, as well as developments in safety, risk assurance, and cybersecurity in both civilian and military contexts. Indeed, rapid progress in developments in the ambient intelligence, including cognitive computing, modeling, and simulation, as well as smart sensor technology, weaves together the human and artificial intelligence and will have a profound effect on the nature of their collaboration at both the individual and societal levels in the near future. As applications of artificial intelligence and cognitive computing become more prevalent in our daily lives, they also bring new social and economic challenges and opportunities that must be addressed at all levels of contemporary society. Many of the traditional human jobs that require high levels of physical or cognitive abilities, including human motor skills, reasoning, and decision-making abilities, as well as training capacity, are now being automated. While such trends might boost economic efficiency, they can also negatively impact the user experience and bring about many unintended social consequences and ethical concerns. The intelligent human systems integration is, to a large extent, affected by the forces shaping the nature of future computing and artificial system development. This book discusses the needs and requirements for the symbiotic collaboration between humans and artificially intelligent systems, with due consideration of the software and hardware characteristics allowing for such cooperation from the societal and human-centered design perspectives, with the focus on the design of intelligent products, systems, and services that will revolutionize future human– technology interactions. This book also presents many innovative studies of ambient artificial technology and its applications, including the human–machine interfaces with a particular emphasis on infusing intelligence into the development of technology throughout the lifecycle development process, with due consideration of user experience and the design of interfaces for virtual, augmented, and mixed reality applications of artificial intelligence. Reflecting on the above-outlined perspective, the papers contained in this volume are organized into seven main sections, including:
1. Automotive design and transportation engineering
2. Humans and artificial cognitive systems
3. Intelligence, technology, and analytics
4. Computational modeling and simulation
5. Humans and artificial systems complexity
6. Materials and inclusive human systems
7. Human–autonomy teaming
8. Applications and future trends
We would like to extend our sincere thanks to Axel Schulte, Stefania Campione,and Marinella Ferrara, for leading a part of the technical program that focuses on human–autonomy teaming and smart materials and inclusive human systems. Our appreciation also goes to the members of Scientific Program Advisory Board who have reviewed the accepted papers that are presented in this volume, including the following individuals:
D. Băilă, Romania
H. Blaschke, Germany
S. Campione, Italy
J. Chen, USA
G. Coppin, France
M. Draper, USA
A. Ebert, Germany
M. Ferrara, Italy
M. Hou, Canada
M. Jipp, Germany
E. Karana, The Netherlands
A. Kluge, Germany
D. Lange, USA
S. Lucibello, Italy
E. Macioszek, Poland
M. Neerincx, The Netherland
2020
- Modular Car Seat for Monitoring the Pressure Distribution on Regions of Pan and Backrest
[Relazione in Atti di Convegno]
Vergnano, A.; Piras, A.; Leali, F.
abstract
Car driver and occupants monitoring is important for safety and comfort. The systems using vision sensors for monitoring the line of sight can be integrated with pressure sensors embedded in the seats to identify critical Out of Position conditions. A new modular car seat is here proposed to monitor the pressure distribution on different significant regions. The solution improves the limitations of existing technologies embedded in seats. The proportional and fast measurement enables online complex evaluations, while the layout reduces the risk of errors. The experiments proved the effectiveness of the prototype.
2020
- Relazioni tra prestazione visiva, abilità motoria e attività fisica in soggetti in età scolare
[Articolo su rivista]
Campa, Francesco; Vergnano, Alberto; Toni, Rita; Lucia Calogero, Angela
abstract
L'attività fisica garantisce benefici relativi allo stato di salute e agli aspetti comportamentali (Strong et al., 2005; Marcus et al., 2006; Physical Activity Guidelines Advisory Committee, 2008), mentre l’assenza di movimento può portare a un decremento della qualità della vita e
a un aumento di patologie gravi e mortalità (Kaplan et al., 1987; Grand et al., 1990; Lynch et al., 2008).
Durante l’infanzia avviene l’apprendimento degli schemi motori di base che rappresentano l’espressione del movimento e vengono considerati la base per la creazione del movimento specializzato (Gallahue & Ozmun, 2006; Clark & Metcalfe, 2002). In particolare, negli ultimi anni, è stata studiata la coordinazione motoria in associazione con la quantità di attività fisica svolta e la maggior parte degli Autori hanno riscontrato una relazione (Graf et al., 2014; Fisher et al., 2005; Castelli & Valley, 2007; Erwin & Castelli, 2008).
Nel presente studio sono state valutate anche le abilità visive, poiché è dimostrato come problematiche visive nei soggetti tendano a essere correlate con una minor pratica di attività sportiva (Kozub & Oh, 2004). L’obiettivo dell’evidenza era quello di analizzare i valori di performance visivi e motori e la loro relazione con la tipologia e la quantità di attività fisica praticata in soggetti in età scolare.
2020
- Robust Parameter Analysis of Compliant Part Models for Computer Aided Tolerancing
[Relazione in Atti di Convegno]
Vergnano, Alberto; Gherardini, Francesco; Petruccioli, Andrea; Bonazzi, Enrico; Leali, Francesco
abstract
Sheet metal parts are widely used in automotive, aerospace, ship and consumer goods industries. The final dimensions of a sheet metal assembly result from the parts deformation, which in turn is affected by many variations in material, thickness and single parts dimensions. The tolerance analysis on sheet metal assemblies improve the knowledge about the process. Advanced simulations enable the optimization of product features, GD&T scheme and assembly process. Moreover, Variational Models of both the product and the assembly system enable to assess the sources of 3D error propagation from the different contributors. However, the simulation results are very affected by the modelling approach of critical components, such as the Fixture Systems. The present paper firstly introduces a strategy to model the Fixture System and the assembly process for compliant parts. Then, a robust analysis of the variations in the model with respect to the modelling factors is performed by a Design of Experiments. A case study on an automotive fender is discussed. The results
demonstrate that the modelling strategy of the clamping operation have the main effects, while the modelling of locators scheme, spot joints and FEM meshing
are less important.
2020
- Sensor matrix robustness for monitoring the interface pressure between car driver and seat
[Relazione in Atti di Convegno]
Vergnano, A.; Muscio, A.; Leali, F.
abstract
An effective sensor system for monitoring the pressure distribution on a car seat would enable researches on Advanced Driver Assistance Systems (ADAS) and comfort of occupants. However, the irregularities of the seat shape or those of the occupant clothes challenge the robustness of such a sensor system. Moreover, the position identification of bodies of different percentiles by few pressure sensors is difficult. So, a higher resolution pressure pad has been developed. The number of sensors is significantly increased by means of a matrix scan strategy. Tests on the pressure pad with different occupants proves its robustness in scanning the contact area.
2020
- The Systematic Design of Industrial Products through Design Archetypes: An Application on Mechanical Transmissions
[Articolo su rivista]
Vergnano, Alberto; Gherardini, Francesco; Leali, Francesco
abstract
Engineering design is a knowledge intensive activity for both new and mature technical systems, such as mechanical transmissions. However, design knowledge is often transferred with conservative and unstructured approaches, although knowledge management would be of the utmost importance for modern industries. In this work, we introduce a design tool, called design archetype, for collecting and managing knowledge in systematic design processes. The design archetype addresses input design requirements for different design concepts, therefore, improving awareness of the design process by interactively modifying the design solution due to different input requirements. Finally, the design archetype updates the parameters of a first embodiment computer-aided design model of the concept. A method for the development of design archetypes is presented and applied to two case studies of mechanical transmission subassemblies. The results demonstrate the effectiveness of a systematic design method based on design archetypes stored in the company database.
2020
- Visual and Motor Capabilities of Future Car Drivers
[Relazione in Atti di Convegno]
Tripi, Ferdinando; Toni, Rita; Lucia Calogero, Angela; Maietta Latessa, Pasqualino; Tempesta, Antonio; Toselli, Stefania; Grigoletto, Alessia; Varotti, Davide; Campa, Francesco; Manzoni, Luigi; Vergnano, Alberto
abstract
Driving safety is recognized as critical for young people by institu-tions, insurances and research. The ability to manage such a complex activity as driving is still developing through adolescence and in early adulthood. The present research investigates the human factors in the driver-car interaction. The experimental method assesses the visual-motor coordination capabilities of future drivers, also in relation to their life styles. The results show that a frequent but good quality physical activity improves visual-motor coordina-tion.
2019
- Correlation of Driver Head Posture and Trapezius Muscle Activity as Comfort Assessment of Car Seat
[Relazione in Atti di Convegno]
Vergnano, A.; Pegreffi, F.; Leali, F.
abstract
Car design must very care comfort and driving pleasure. Nonetheless, the design choices are tested with subjective evaluations. In the present research, an objective measurement equipment for driving comfort assessment is proposed. The muscles activity of the driver in different maneuvers is considered the gauge of her/his feeling with the car. The activity of trapezius muscles of both shoulders is monitored by electromyography (EMG), through electrodes applied to her/his skin. The driver posture is monitored with a robust device for head tracking, using two 9-axis orientation sensors, including gyroscope. Real driving experiments are performed both with a luxury SUV and a high-end car. As expected, the first resulted more comfortable. The proposed equipment proved to be effective in assessing the driving comfort for different seat designs and car layouts.
2019
- Efficiency and reliability of gravity die casting models for simulation based design
[Relazione in Atti di Convegno]
Vergnano, A.; Brambilla, E.; Bonfiglioli, G.
abstract
Simulation of Gravity Die Casting (GDC) requires to couple different models for fluid dynamics, heat transfer and solidification, together with material physics properties. Very long calculation times are required since several heating and production cycles have to be run. The simplification of the simulation models is critical to have results in useful times for the design process. The present work discusses the solidification and heat transfer physics with simplification hypoth-eses. A simulation approach skipping the pouring model for the heating cycles is introduced. A realistic case study on an engine head GDC is presented to evalu-ate four possible simulation sequences. The results show that including the heat-ing cycles in the simulation is advisable. The simplified sequences reproduce the temperature field of the die with sufficient accuracy. The proposed simulation approach results in considerable time savings with respect to the actual simula-tions and even in little accuracy improvements.
2019
- Monitoring Driver Posture Through Sensorized Seat
[Relazione in Atti di Convegno]
Vergnano, A.; Leali, F.
abstract
Future intelligent vehicles will be capable to monitor driver distraction while autonomous driving. However, in case of system fault, the intelligent vehicle must also manage an adaptive strategy for the Airbag Control Unit, since the airbag deployment against an Out of Position occupant can be additionally harmful. Thus, the present research work investigates a possibility to monitor the driver position as a robust information to an intelligent vehicle. A seat is sensorized with a map of pressure sensors. The system layout and setup are discussed in details. Signal processing strategy and real driving experiments are reported.
2019
- Out of Position Driver Monitoring from Seat Pressure in Dynamic Maneuvers
[Relazione in Atti di Convegno]
Vergnano, A.; Leali, F.
abstract
An airbag system is designed to reduce the accident outcome on the car occupants. The airbags deployment against manikins is severely tested according to international regulations. The accident scenarios with Out of Position (OP) occupants are critical since they can be hardly expected during design. The airbag deployment in these scenarios can be improved by developing adaptive strategies, provided that the Airbag Control Unit must be aware of the actual occupant position. The present research investigates a sensor system to monitor the occupants in an interactive Human-Car system. The driver position is monitored by pressure sensors, while an accelerometer enables to compensate for acceleration and noise. Real driving experiments in dynamic conditions are reported. The results prove that three OP conditions are effectively identified.
2019
- Real Time Kinematic and Electromyographic Analysis: a Feasible Methodology for Assessing Comfort Perception
[Relazione in Atti di Convegno]
Pegreffi, F.; Muraccini, M.; Berardi, A.; Varini, A.; Vergnano, A.; Leali, F.; Mantovani, M.
abstract
Driving comfort is a key emerging factor for the marketability of cars due to the growing interest in the evaluation of ergonomics in cars. Typical ergonomic issues, related to the locomotor system, happens when the muscular effort is too high to perform the task or kinematics is too restricted [MARE]. The ergonomic evaluation identifies the critical aspects of the steering task and intervenes to reduce injuries, thus increasing the driver's well-being. The subjective evaluation of driving comfort is still the most used way to design a car seat; this limitation could be overcome by using emerging technologies [MARE]. The activity of trapezius muscles of both shoulders is assumed as predicting factor of car seat comfort while driving. The present research aims to analyze the feasibility of kinematic analysis and muscle activity during car driving in terms of quantitatively detecting trapezius muscle activity in real-time condition.
2019
- SEDILE DI VEICOLO CON SISTEMA DI RILEVAMENTO PASSEGGERI
[Brevetto]
Vergnano, A.; Piras, Andrea; Leali, F.
abstract
È descritto un sedile di veicolo con sistema di rilevamento passeggeri, comprendente una pluralità di sensori di forza (11) distribuiti 5 superficialmente su almeno un substrato (1), sostenuto da un telaio (F) del sedile oppure facente esso stesso funzione di telaio, in risposta alla sollecitazione del peso dell'occupante del sedile e dei suoi sforzi durante la guida, un cablaggio (12) 10 collegato elettricamente a ciascun sensore di forza (11), almeno una scatola di giunzione (2), il cablaggio (12) collegato elettricamente alla scatola di giunzione (2), un cablaggio comune (21) collegato elettricamente alla scatola di giunzione (2), il 15 cablaggio comune (21) adattato per essere collegato ad un controllore del veicolo (3) per fornire un segnale elettrico. Una pluralità di porzioni rigide di supporto (4) è interposta tra i sensori di forza (11), a loro volta sostenuti dal substrato (1), ed 20 almeno uno strato di imbottitura (5).
2017
- Design Archetype of Gears for Knowledge Based Engineering
[Relazione in Atti di Convegno]
Peroni, Mariele; Vergnano, Alberto; Leali, Francesco; Brentegani, Andrea
abstract
An engineering design process consists of a sequence of creative, innovative and routine design tasks. Routine tasks address well-known procedures and add limited value to the technical improvement of a product, even if they may require a lot of work. In order to focus designers work on added value tasks, the present work aims at supporting a routine task with a Design Archetype (DA). A DA captures, stores and reuses the design knowledge with a tool embedded in a CAD software. The DA algorithms drive the designer in selecting the most effective design concept to deliver the project requirements and then embody the concept through configuring a CAD model. Finally, a case study on the definition of a DA tool for gear design demonstrates the effectiveness of the DA tool.
2017
- Integrated design method for optimal tolerance stack evaluation for top class automotive chassis. In Advances on Mechanics, Design Engineering and Manufacturing (pp. 1013-1022). Springer International Publishing.
[Relazione in Atti di Convegno]
Panari, Davide; Renzi, Cristina; Vergnano, Alberto; Bonazzi, Enrico; Leali, Francesco
abstract
The tolerances of welded chassis are usually defined and adjusted in very expensive trials and errors on the shop floor. Computer Aided Tolerancing (CAT) tools are capable to optimize the tolerances of given product and process. However, the optimization is limited since the manufacturing process is already mostly defined by the early choices of product design. Therefore, we propose an integrated design method that considers the assembly operations before the detail design of the chassis and the concept design of the fixture system. The method consists in four phases, namely functional analysis in the CAD environment, assembly sequence modelling in the CAT tool, Design Of Simulation Experiment on the stack of the tolerance ranges and finally optimization of the tolerances. A case study on a car chassis demonstrates the effectiveness of the method. The method enables to selectively assign tight tolerances only on the main contributors in the stack, while generally requiring cheaper assembly operations. Moreover, a virtual fixture system is the input for the assembly equipment design as on optimized set of specifications, thus potentially reducing the number of trials and errors on the shop floor.
2017
- Interactive simulation-based-training tools for manufacturing systems operators: an industrial case study
[Articolo su rivista]
Vergnano, Alberto; Berselli, Giovanni; Pellicciari, Marcello
abstract
Industrial process plants are increasingly becoming complex structures with high level of automation. Nonetheless, the final plant productivity and the overall equipment efficiency does not solely depend on an optimized engineering design/installation practice, but also on human operators supervision. In parallel, along with the classic demand to minimize costs and time-to-market during the design phases, issues concerning human safety and failure prevention play a crucial role, one of the highest target being the avoidance of dangerous process states. Within this context, Simulation-Based-Training (SBT) allows plant operators to learn how to command complex automated machineries within a secure virtual environment. Similar to its usage in medical, aerospace, naval and military fields, SBT for manufacturing systems can be employed in order to involve the user within a realistic scenario, thus providing an effective, lifelike, interactive training experience under the supervision of experienced personnel. In addition, also according to previous literature, industry-driven SBT may be effectively envisaged as a natural extension of the plant life-cycle simulation practice, comprising Design Simulation & Optimization, Virtual Commissioning, Operator Training, up to Plant Maintenance. In this context, since the overall system behavior depends both on manufacturing process dynamics and Control Logics, the main challenge for an effective SBT is related with the development of a real-time environment where control system responsiveness is fully reproduced. Owing to this consideration, this paper reports a successful industrial case study, concerning a novel SBT workbench used for steel plants operator training, discussing both the virtual prototyping phase and the development of a real-time simulation architecture. In particular, a hybrid process simulation is employed, where a virtual process model is coupled with physical PLC and Human–Machine Interface, thus achieving an accurate reproduction of the real plant/operator interaction.
2017
- Numerical Simulation and Experimental Validation of MIG Welding of T-Joints of Thin Aluminum Plates for Top Class Vehicles
[Articolo su rivista]
Bonazzi, Enrico; Colombini, Elena; Panari, Davide; Vergnano, Alberto; Leali, Francesco; Veronesi, Paolo
abstract
The integration of experiments with numerical simulations can efficiently support a quick evaluation of the welded joint. In this work, the MIG welding operation on aluminum T-joint thin plate has been studied by the integration of both simulation and experiments. The aim of the paper is to enlarge the global database, to promote the use of thin aluminum sheets in automotive body industries and to provide new data. Since the welding of aluminum thin plates is difficult to control due to high speed of the heat source and high heat flows during heating and cooling, a simulation model could be considered an effective design tool to predict the real phenomena. This integrated approach enables new evaluation possibilities on MIG-welded thin aluminum T-joints, as correspondence between the extension of the microstructural zones and the simulation parameters, material hardness, transient 3D temperature distribution on the surface and inside the material, stresses, strains, and deformations. The results of the mechanical simulations are comparable with the experimental measurements along the welding path, especially considering the variability of the process. The results could well predict the welding-induced distortion, which together with local heating during welding must be anticipated and subsequently minimized and counterbalance.
2017
- Parametric virtual concepts in the early design of mechanical systems: a case study application
[Articolo su rivista]
Vergnano, Alberto; Berselli, Giovanni; Pellicciari, Marcello
abstract
Virtual prototyping enables the validation and optimization of mechanical devices similar to physical testing, saving time and costs in the product development, especially in case of heavy machines with complex motions. However, virtual prototyping is usually deployed only at the end of the design process, when the product architecture has already been developed. The present paper discusses the introduction of virtual prototypes since the conceptual design stage as “Virtual Concepts”, in which coarse models of machinery design variants are simulated obtaining useful information, sometimes fundamental to support best design choices. Virtual Concept modeling and preliminary validation, along with its later integration into a Virtual Prototype, are expressly investigated using Multi Body Dynamics software. A verification case study concerning a large vibrating screen is presented, in order to demonstrate that dynamic Virtual Concepts can enable an easier and effective evaluation of the design variants, thus increasing the design process predictability. Finally, current challenges to be solved for the practical adoption of Virtual Concept simulations as an integral part of the industrial design process are critically discussed.
2016
- A workcell calibration method for enhancing accuracy in robot machining of aerospace parts
[Articolo su rivista]
Leali, Francesco; Vergnano, Alberto; Pini, Fabio; Pellicciari, Marcello; Berselli, Giovanni
abstract
Industrial robotics provides high flexibility and reconfigurability supported by a user-friendly programming, but still lacks in accuracy. An effective workcell calibration reduces errors in robot manufacturing and enables robot machining applications. A novel workcell calibration method is embedded in an integrated design framework for an in-depth exploitation of CAD-based simulations and offline programming. The method is composed of two steps: first calibration of the workpiece-independent equipment in the workcell layout and final automated online calibration of workpiece-dependent equipment. The method is finally applied to a changeable robotic workcell for finishing aluminium cast housings for aerospace gear transmissions characterised by complex shapes and by close dimensional and geometrical specifications. Experimental results prove the method effectiveness in enhancing accuracy in robot machining.
2016
- ANOVA OF 3D VARIATIONAL MODELS FOR COMPUTER AIDED TOLERANCING WITH RESPECT TO THE MODELING FACTORS
[Relazione in Atti di Convegno]
Bonazzi, Enrico; Vergnano, Alberto; Leali, Francesco
abstract
Sheet metal assemblies are subjected to errors as deformations due to material, thickness, geometries and process variations. Advanced simulations enable the optimization of product features, GD&T scheme and assembly process. The 3D error propagation due to the different contributors can be studied with Variational Models of the product and assembly system. However, the practical application of these methods is limited by the high number of factors in the models, which makes the operator experience fundamental to achieve their trustworthiness. Guidelines for modeling the sheet metal assemblies are needed. The present work aims at analysing the variations in the model with a Design of Computer Experiments (DoCE) plan. A case study on an automotive fender is discussed. The results demonstrate that the modeling strategy of clamping operation have the major effects, while the modeling of locators scheme, spot joints and FEM meshing are less important.
2016
- DESIGN ARCHETYPE OF TRANSMISSION CLUTCHES FOR KNOWLEDGE BASED ENGINEERING
[Relazione in Atti di Convegno]
Peroni, Mariele; Vergnano, Alberto; Leali, Francesco
abstract
The management of technical knowledge in engineering
design is a key target for nowadays industry. Accessibility to
knowledge by designers and standardization of models are still
open issues to be fixed with integrated solutions. The present
paper proposes a methodological support for keeping the value
of designers’ experience in the company with Knowledge Based
Engineering. A Design Archetype (DA) is developed to simply
store and reuse the knowledge during the execution of the design
tasks. The DA drives designers in selecting the most suitable
working principles to address the project requirements and in
dimensioning the subsystems, providing an embodiment CAD
model. The applicability of the proposed methodology in
industry is demonstrated for the design of clutches of agricultural
tractor transmissions.
2016
- REDESIGN FOR ENVIRONMENT OF WOODEN PACKAGING FOR BULK RECYCLING AND RECOVERY. ARPN Journal of Engineering and Applied Sciences VOL. 11, NO. 1, JANUARY 2016.
[Articolo su rivista]
Vergnano, Alberto; Renzi, Cristina; Leali, Francesco
abstract
Society increasingly demands for effective waste management policies to make industries more environmentally
sustainable. Organizations are even issuing directives to drive choices about these policies. In particular, modern industries
produce a lot of packaging, which soon become waste, even before product usage. Research can face the problem with
improvements in recycling and recovery processes. However, even if recycling and recovery would enable waste to have
still a value, most costs and benefits are determined at the design stage. Therefore, Design for Environment criteria must be
adopted in the design tasks, from the early conceptual design when the main design solutions are defined. The design
criteria to assess possible design choices must consider all the environmental impacts of packaging over its lifecycle. The
present work focuses on Redesign for Environment of packaging solutions. Following a systematic design process, we use
different criteria to evaluate the effects of design solutions on packaging, since waste can be seen just as one of the main
phases of packaging life. To this purpose, we adopt the stages of the waste hierarchy set by the EU Waste Framework
Directive 2008/98/EC as design evaluation criteria. The waste hierarchy sets a priority order for five life cycle stages that a
packaging can go through. The stages of the hierarchy can be differently weighted according to the costs and benefits they
involve. The proposed Design for Environment method based on the waste hierarchy criteria is finally applied in the
redesign of an industrial case study. The packaging solution as foldable wooden crates were chosen for their capability to
already comply with the first stages of the hierarchy, that is reducing waste with high customization to customer
requirements and crate reuse. Hence, the case study improved the next stages with easing the wood recycle and recovery
processes
2014
- Hardware in the Loop Simulation-Based Training for Automated Manufacturing Systems Operators
[Relazione in Atti di Convegno]
Vergnano, Alberto; Pellicciari, Marcello; Berselli, Giovanni
abstract
Simulation-Based-Training (SBT) allows to train the operators of complex machinery within a safe virtual environment by means of effective lifelike learning experiences. SBT has been efficiently used in medical, aerospace and military fields and it may provide a competitive advantage also for the training of operators in mechatronic plants. In fact, at the current state of the art, human-machine interaction still heavily impacts on the final performances of automated plants. Since the fast-evolving process dynamics of the machinery is controlled and supervised by complex software logics, the main challenge for effective and valid SBT concerns the development of a real-time simulation, where the control system responsiveness is fully reproduced. This paper deals with a novel SBT workbench used for steel plants operator training, discussing the real-time simulation architecture developed for the purpose. Following a hybrid process simulation approach, real-time control Hardware-In-the-Loop technology assures seamless and accurate reproduction of the real plant, also achieving the desired Man-in-the-Loop practice for the operator interaction. A conceptual architecture for a virtual interactive prototype is proposed, including controllers and interfaces for trainer and trainees. A case study on an electric arc furnace is implemented within a Virtual Commissioning tool, analyzing its capabilities and limitations
2014
- Hardware-in-the-Loop Mechatronic Virtual Prototyping of a High-Speed Capsule Filling Machine
[Relazione in Atti di Convegno]
Pellicciari, Marcello; Vergnano, Alberto; Berselli, Giovanni
abstract
In the field of pharmaceutical processing, last generation automatic machines autonomously modify their behavior in order to achieve the best manufacturing quality and productivity despite ever changing process requirements. Mechatronics, as a synergistic integration of electro-mechanical equipment and software control logics, enables such adaptive self-optimizing behaviors. Unfortunately, due to the complex interactions between the different technologies, the final performance of these systems can be effectively validated and optimized only on a physical prototype, with limited possibilities to introduce possible design changes. Therefore, in order to enable validation/optimization of high performance machinery during engineering design stage, a mechatronic Virtual Prototyping (VP) technology is strongly needed. Within this context, the present work discusses a mechatronic VP method based on a Hardware-in-the-Loop, hybrid-process simulation approach, where interactive real-time simulations can effectively assess the real final performance under changing process scenarios. In particular, a case study concerning a high-speed automatic machines for pharmaceutical capsules filling is
thoroughly discussed.
2014
- Parametric virtual concept design of heavy machinery: a case study application
[Relazione in Atti di Convegno]
Vergnano, Alberto; Pellicciari, Marcello; Berselli, Giovanni
abstract
Virtual prototyping enables the validation and optimization of machinery equivalent to physical testing, saving time and costs in the product development, especially in case of heavy machines with complex motions. However, virtual prototyping is usually deployed only at the end of the design process, when product architecture is already developed. The present paper discusses the introduction of virtual prototypes since conceptual design stage as Virtual Concepts in which coarse models of machinery design variants are simulated obtaining useful information, sometimes fundamental to support best design choices. Virtual Concept modeling and preliminary validation and its later integration to a Virtual Prototype are expressly investigated using Multi Body Dynamics software. A verification case study on a large vibrating screen demonstrates that dynamic Virtual Concepts enable easier and effective evaluations on the design variants and increase the design process predictability.
2013
- A Calibration Method for the Integrated Design of Finishing Robotic Workcells in the Aerospace Industry
[Relazione in Atti di Convegno]
Leali, Francesco; Pellicciari, Marcello; Pini, Fabio; Vergnano, Alberto; Berselli, Giovanni
abstract
Industrial robotics provides high flexibility and reconfigurability, cost effectiveness and user friendly programming for many applications but still lacks in accuracy. An effective workcell calibration reduces the errors in robotic manufacturing and contributes to extend the use of industrial robots to perform high quality finishing of complex parts in the aerospace industry. A novel workcell calibration method is embedded in an integrated design framework for an in-depth exploitation of CAD-based simulation and offline programming.
The method is composed of two steps: a first offline calibration of the workpiece-independent elements in the workcell layout and a final automated online calibration of workpiece-dependent elements. The method is finally applied to a robotic workcell for finishing aluminum housings of helicopter gear transmissions, characterized by complex and non-repetitive shapes, and by severe dimensional and geometrical accuracy demands. Experimental results
demonstrate enhanced performances of the robotic workcell and improved final quality of the housings.
2013
- A method for reducing the energy consumption of pick-and-place industrial robots
[Articolo su rivista]
Pellicciari, Marcello; Berselli, Giovanni; Leali, Francesco; Vergnano, Alberto
abstract
The interest in novel methods and tools for opt imizing the energy consumption in robotic systems is currently increasing. From an industrial point of view, it is desirable to develop energy saving strategies also applicable to established manufacturing systems with no need for either hardware substitution or further investments. Within this scenario, the present paper reports a method for reducing the total energy consumption of pick-and-place manipulators for given TCP position profiles. Firstly, electromechanical mod-els of both serial and parallel manipulators are derived. Then, the energy-optimal trajectories are calculated, by means of constant time scaling, starting from pre-scheduled trajectories compatible with the actuation limits. In this manner, the robot work cycle can be energetically optimized also when the
TCP position profiles have been already defined on the basis of technological constraints and/or design choices aimed at guarante eing manufacturing process efficacy/robustness. The effectiveness of the proposed procedure is finally evaluated on two simulation case studies.
2013
- An Offline Programming Method for the Robotic Deburring of Aerospace Components
[Relazione in Atti di Convegno]
Leali, Francesco; Pellicciari, Marcello; Pini, Fabio; Berselli, Giovanni; Vergnano, Alberto
abstract
Deburring of aerospace components is a complex task in case of large single pieces designed and optimized to deliver many mechanical functions. A constant high quality requires accurate 3D surface contouring operations with engineered tool compliance and cutting power. Moreover, aeronautic cast part production is characterized by small lot sizes with high variability of geometries and defects. Despite robots are conceived to provide the necessary flexibility, reconfigurability and efficiency, most robotic workcells are very limited by too long programming and setup times, especially at changeover. The paper reports a design method dealing with the integrated development of process and production system, and analyzes and compares a CAD-based and a digitizer based offline programming strategy. The deburring of gear transmission housings for aerospace applications serves as a severe test field. The strategies are compared by the involved costs and times, learning easiness, production downtimes and machining accuracy. The results show how the reconfigurability of the system together with the exploitation of offline programming tools improves the robotic deburring process.
2013
- Efficient Simulation of Single Degree of Freedom Servomechanisms for Automatic Machines
[Relazione in Atti di Convegno]
Vergnano, Alberto; M., Marsala; Costantino, Antonio; F., Balugani
abstract
An automatic manufacturing system design must be optimized with a simulation including all the interacting devices. The simulation should be controlled by the real control system with a hardware in the loop approach. So the techniques for modeling the mechanisms must be effective for the model to be run without violating the real-time protocol. This paper reports a method to model the motor load by means of a reduced moment of inertia, where all the part downstream from the motor output shaft is transformed in function of the only one mechanism degree of freedom. The resulting model behaves as the real nonlinear mechanism, but it is computationally efficient since it is not ruled by the multibody 3D CAD mathematics.
2013
- High Level Scheduling of Energy Optimal Trajectories
[Articolo su rivista]
O., Wigstrom; B., Lennartson; VERGNANO, ALBERTO; C., Breitholtz
abstract
The reduction of energy consumption is today addressed with great effort in manufacturing industry. In this paper, we improve upon a previously presented method for robotic system scheduling. By applying dynamic programming to existing trajectories, we generate new energy optimal trajectories that follow the same path but in a different execution time frame. With this new method, it is possible to solve the optimization problem for a range of execution times for the individual operations, based on one simulation only. The minimum energy trajectories can then be used to derive a globally energy optimal schedule. A case study of a cell comprised of four six-link manipulators is presented, in which energy optimal dynamic time scaling is compared to linear time scaling. The results show that a significant decrease in energy consumption can be achieved for any given cycle time.
2012
- Hybrid Reconfigurable System design and optimization through virtual prototyping and digital manufacturing tools
[Articolo su rivista]
Andrisano, Angelo Oreste; Leali, Francesco; Pellicciari, Marcello; Pini, Fabio; Vergnano, Alberto
abstract
Engineering changeability-oriented and cost-driven approaches are needed by enterprises to design and optimize manufacturing and assembly systems for the demanding production requirements of the present industrial scenario. The integrated design of Reconfigurable Systems addresses tailored flexibility through modularity, integrability of resources, product and process customization, and system convertibility and diagnosability. The cooperation of robot and humans in hybrid environments offers a good trade-off between changeability, high quality and low costs, by exploiting the human dexterity and cognitive proactivity, together with robotic accuracy and performances. Virtual prototyping methods and digital manufacturing solutions are now mature and effective enough to play a strategic role within the hybrid reconfigurable system (H-RS) design and optimization process. The present research work proposes an engineering method to design and optimize H-RSs, by using virtual prototyping and digital manufacturing as a strategic support for the analysis and synthesis of the technical solutions, especially those related to human-robot cooperation. An industrial case study on a hybrid reconfigurable assembly system of a top class car aluminum chassis is finally presented.
2012
- Increasing the Energy Efficiency of Multi-robot Production Lines in the Automotive Industry
[Relazione in Atti di Convegno]
D., Meike; Pellicciari, Marcello; Berselli, Giovanni; Vergnano, Alberto; L., Ribickis
abstract
This paper quantitatively reports bout potential
energy savings on robotic assembly lines for the automotive
industry. The key aspect of the proposed approach is that
both cell production rate and robot hardware limitations are
consideredasstrictconstraints,sothatnoplantrevisionis
needed. The methodology relies on: a)calculationofenergy-
optimal trajectories, by means of time scaling, concerning the
robots’ motion from the last process point to the home positions;
b)reduction o f the energy consumption vi aearlier release of the
actuator brake whentherobotsarekeptstationary. Simulation
results arepresented,whicharebasedontheproductiontiming
characteristicsmeasuredonarealplant.
2012
- Metodo di progettazione di sistemi di fixture per l’assemblaggio di telai automobilistici mediante analisi di sensibilità
[Relazione in Atti di Convegno]
Andrisano, Angelo Oreste; Ansaloni, Matteo; Berselli, Giovanni; Bonazzi, Enrico; Gherardini, Francesco; Leali, Francesco; Pellicciari, Marcello; Pini, Fabio; Renzi, Cristina; Vergnano, Alberto
abstract
I sistemi di fixture influenzano enormemente i processi di assemblaggio in molti campi della meccanica, in quanto influiscono direttamente sul calcolo della catena di tolleranza. La memoria illustra un metodo di progettazione che permette di comparare e valutare differenti sistemi di fissaggio, considerando sia la posizione che il tipo di locatori. Poiché i sistemi di fixture possono essere considerati dei sistemi multi-prestazionali, il confronto viene eseguito attraverso l’impiego di opportuni indici di sensibilità. Il metodo è
stato applicato ad un caso di studio in ambito automotive relativo alla saldatura in continuo di estrusi in allumino, con l’obiettivo di garantire misure di gap con la minore variabilità possibile.
2012
- Modeling and Optimization of Energy Consumption in Cooperative Multi-Robot Systems
[Articolo su rivista]
Vergnano, Alberto; C., Thorstensson; B., Lennartson; P., Falkman; Pellicciari, Marcello; Leali, Francesco; S., Biller
abstract
Reduction of energy consumption is important for reaching a sustainable future. This paper presents a novel method for optimizing the energy consumption of robotic manufacturing systems. The method embeds detailed evaluations of robots' energy consumptions into a scheduling model of the overall system. The energy consumption for each operation is modeled and parameterized as function of the operation execution time, and the energy-optimal schedule is derived by solving a mixed-integer nonlinear programming problem. The objective function for the optimization problem is then the total energy consumption for the overall system. A case study of a sample robotic manufacturing system and an experiment on an industrial robot are presented. They show that there exists a real possibility for a significant reduction of the energy consumption in comparison to state-of-the-art scheduling approaches.
2012
- Object-oriented modeling of industrial manipulators with application to energy optimal trajectory scaling
[Relazione in Atti di Convegno]
Pellicciari, Marcello; Berselli, Giovanni; Leali, Francesco; Vergnano, Alberto; B., Lennartson
abstract
The development of safe, energy efficient mechatronic sys-tems is currently changing standard paradigms in the design andcontrol of industrial manipulators. In particular, most optimiza-tion strategies require the improvement or the substitution of dif-ferent system components. On the other hand, from an indus-try point of view, it would be desirable to develop energy savingmethods applicable also to established manufacturing systemsbeing liable of small possibilities for adjustments. Within thisscenario, an engineering method is reported for optimizing theenergy consumption of serial manipulators for a given operation.An object-oriented modeling technique, based on bond graph, isused to derive the robot electromechanical dynamics. The systempower flow is then highlighted and parameterized as a function ofthe total execution times. Finally, a case study is reported show-ing the possibility to reduce the operation energy consumptionwhen allowed by scheduling or manufacturing constraints.
2011
- A Minimal Touch Approach for Optimizing Energy Efficiency inPick-and-Place Manipulators
[Relazione in Atti di Convegno]
Pellicciari, Marcello; Berselli, Giovanni; Leali, Francesco; Vergnano, Alberto
abstract
The interest in novel engineering methods andtools for optimizing the energy consumption in robotic systemsis currently increasing. In particular, from an industry pointof view, it is desirable to develop energy saving strategiesapplicable also to established manufacturing systems, beingliable of small possibilities for adjustments.Within this scenario,an engineering method is reported for reducing the totalenergy consumption of pick-and-place manipulators for givenend-effector trajectory. Firstly, an electromechanical model ofparallel/serial manipulators is derived. Then, an energy-optimaltrajectory is calculated, by means of time scaling, starting froma pre-scheduled trajectory performed at maximum speed (i.e.compatible with actuators limitations). A simulation case studyfinally shows the effectiveness of the proposed procedure.
2011
- A novel method for sensitivity analysis and characterization in integrated engineering design
[Relazione in Atti di Convegno]
Andrisano, Angelo Oreste; Ansaloni, Matteo; Leali, Francesco; Pellicciari, Marcello; Vergnano, Alberto
abstract
Purpose:The present research work aims to analyze and characterize processes in terms of sensitivity of their performances. Robust design techniques, generally adopted for product and process optimization, are not suited for investigating sensitivity. Then a novel approach to such engineering problem needs to be proposed.Method:The developed method integrates and extends to the analysis of manufacturing and technological processes the Performance Sensitivity Distribution (PSD) theory, primarily introduced to provide analytical and geometric description of performance sensitivity for robotic mechanisms.Result:Such novel method, named Specialized PSD, starts from the clarification of the sensitivity analysis problem by defining key parameters, i.e. Design Variables (DVs), Design Parameters (DPs) and Performance Functions (PFs). According to the PSD theory, PF sensitivity is expressed in terms of deviations of DVs and DPs and it is geometrically described by a hyperellipsoid in the n-dimensional space. Sensitivity indexes are then introduced to assess PF variation for different combinations of DVs and DPs deviations. Regression Analysis is adopted to provide the mathematical description of PFs so the PSD theory is finally specialized to be applied in a process sensitivity analysis. Injection molding of a plastic specimen is finally investigated to validate the proposed method.Discussion & Conclusion:This work specialize the PSD theory for manufacturing and technological processes, extending its original field of application thanks to a novel approach to the analytical expression of the PFs. Moreover, when 2 or 3 parameters are considered, sensitivity indexes are graphically represented through tolerance maps of colour, so the method can be easily adopt for integrated design, especially in the early stage of product and process development.
2011
- Design Of Simulation Experiments method for Injection Molding process optimization
[Relazione in Atti di Convegno]
Andrisano, Angelo Oreste; Gherardini, Francesco; Leali, Francesco; Pellicciari, Marcello; Vergnano, Alberto
abstract
Purpose:Many studies demonstrate that DOE, CAE and optimization tools can be very effective in product and process development, however their integration is still under investigation, hampering the applicability of such engineering methods in Industry. This paper presents a Design Of Simulation Experiments (DOSE) method, developed to determine the optimal set of process parameters (factors) for given product requirements (responses).Method:The method is developed performing an original selection and integration of engineering procedures and techniques based on DOE, CAE and multi-objective optimization, chosen according to the following criteria: ease of application, time-saving and use of reduced resources.Result:The developed method consists of two main steps: a first screening of factors based on a fractional DOE is followed by a systematic experimental plan based on the Response Surface Methodology (RSM), in which only key factors are investigated. A regression model is finally developed to describe the responses as functions of key factors and a multi-objective optimization is proposed to obtain optimal responses by tuning the process factors in their variability range. The DOSE method is finally validated on the design of an injection molded housing for a biomedical application. This thin shell component has dimension 45mmx37mmx16mm, wall thickness from 2mm to 0,5mm and is made of polyphenylsulfone (PPSU), a high performance thermoplastic.Discussion & Conclusion:The design method achieves good responses in terms of dimensional and geometrical requirements (e.g. warpage, shrinkage, sink marks), and improves the shell moldability. The DOSE method can be easily adopted in industrial product/process development to define the optimal process parameters for a better final quality of the products.
2011
- Integrated Design of Robotic Workcells for High Quality Machining
[Relazione in Atti di Convegno]
Andrisano, Angelo Oreste; Leali, Francesco; Pellicciari, Marcello; Pini, Fabio; Vergnano, Alberto
abstract
Purpose:Robotic workcells provide high flexibility and reconfigurability, cost effectiveness and user friendly programming for many industrial applications but still lack in accuracy, so important fields of application such as mechanical machining are currently covered by very expensive and rigid systems (machining centers). The present work investigates the possibility to extend the use of industrial robots to perform high quality machining.Method:The proposed method is focused on the enhancement of robotic machining accuracy through an integrated design method, based on robotic process simulation and tailored design of mechanical apparatus and software modules for robot control and programming. Advanced techniques for machining strategy validation, automatic robot path generation, workcell calibration, robot code commissioning are concurrently adopted.Result:Integrated design tools are fully exploited to define the system behavior, to simulate the whole process, to propose alternative machining set-ups and quickly generate and test parametric programs. The design method is finally applied to design a robotic workcell family for grinding special austenitic manganese steel casts, characterized by severe working conditions as high tool wear, high cutting forces, high vibrations due to surface hardness and non-repetitive shape variations in geometry and features.Discussion & Conclusion:Experimental results demonstrate enhanced performance of robotic workcells and final quality, due to minimization of tool vibration, increasing of robot stiffness and higher manufacturing flexibility, thanks to the capability of adapting robot paths to workpieces.
2011
- Una metodologia innovativa di progettazione integrata per l'analisi e la caratterizzazione della sensitività delle performance
[Relazione in Atti di Convegno]
Andrisano, Angelo Oreste; Ansaloni, Matteo; Gherardini, Francesco; Leali, Francesco; Pellicciari, Marcello; Pini, Fabio; Vergnano, Alberto
abstract
Il presente lavoro è volto all’analisi e alla caratterizzazione della sensitività delle performance dei processi tecnologici. Le tradizionali tecniche di Robust Design utilizzate per l’analisi e l’ottimizzazione di processi e prodotti non sono state sviluppate con l’obiettivo dell’analisi della sensitività e, pertanto, presentano alcune carenze applicative. Il presente articolo propone un approccio alternativo che integra, estendendola ai processi tecnologici, la teoria della Performance Sensitivity Distribution (PSD), originariamente proposta nell’ambito dell’analisi dei meccanismi e, in particolare, nell’analisi dei manipolatori. Questo nuovo approccio, denominato specialized PSD, descrive il problema della sensitività delle performance attraverso la definizione di parametri chiave del progetto, suddivisi in Design Variables (DV) e Design Parameters (DP), e la formalizzazione di Performance Functions (PF). In accordo con la teoria PSD, la sensitività delle PF è espressa in funzione delle deviazioni dei DV e dei DP dai relativi valori nominali: essa è geometricamente descritta da un iperellissoide costruito nello spazio delle deviazioni, e valutata attraverso l’introduzione di indici di sensitività. La complessità nell’estensione dell’approccio PSD all’analisi dei processi tecnologici è legata alla necessità di ottenere la descrizione matematica delle PF in funzione dei parametri di progetto. Il metodo proposto, tuttavia, permette di superare tale problematica mediante un approccio legato all’analisi di regressione su dati sperimentali. Una strategia di Design Of Experiments viene applicata allo studio dei processi, così da campionare il comportamento delle PF in funzione della variazione dei parametri di progetto. Un caso di stampaggio ad iniezione di un provino è riportato al fine della validazione del metodo. In un’ottica di progettazione integrata, il metodo proposto si rivela utile per la caratterizzazione delle performance, specialmente nelle prime fasi di sviluppo di prodotto e processo.
2010
- Automazione e Verifica del Processo di Incollaggio in Linee Produttive di Telai per Vetture d’Alta Gamma
[Abstract in Atti di Convegno]
Andrisano, Angelo Oreste; Baldini, Andrea; Bertocchi, Enrico; Giacopini, Matteo; Leali, Francesco; Mantovani, Sara; Pellicciari, Marcello; Pini, Fabio; Strozzi, Antonio; Vergnano, Alberto
abstract
Sommario. La produzione industriale dei telai auto ha registrato, nel tempo, una grande evoluzione progettuale e tecnologica, spinta dalla necessità di garantire alte prestazioni e comfort elevato, nel rispetto della sicurezza dei passeggeri e della sostenibilità ambientale. Le linee produttive di assemblaggio sono, soprattutto in segmenti di fascia alta, progettate per l‟esecuzione, su telai diversi, di articolati processi ibridi di giunzione, basati, cioè, sull‟adozione di tecnologie di saldatura, rivettatura ed incollaggio. I sistemi che ne derivano sono, dunque, caratterizzati da elevata complessità e richiedono lo sviluppo di dispositivi automatici dedicati e l‟impiego simultaneo di robot industriali e risorse umane. La soluzione di tali problematiche richiede l‟intervento sinergico di vari settori dell‟Ingegneria Meccanica poiché coinvolge competenze metallurgiche, progettuali e tecnologiche. A queste si aggiungono le competenze necessarie alla progettazione di sistemi produttivi ad alta flessibilità che, secondo la visione proposta dagli autori, siano caratterizzati da elevata modularità strutturale ed operativa, parametricità e standardizzazione delle soluzioni progettuali e dei componenti, autonomia esecutiva, e che assicurino una rapida ed efficace riconfigurazione, garantendo, parallelamente, l‟alto livello qualitativo dei prodotti ed il completo controllo dei processi realizzati. Il presente articolo tratta lo sviluppo e la progettazione integrata del modulo robotizzato di incollaggio per linee di assemblaggio ibride di telai in alluminio, svolta in collaborazione con il gruppo ALCOA e con SIR SpA. Successivamente vengono presentati i risultati sperimentali ottenuti dalla verifica strutturale a lap shear e peeling di alcuni provini ricavati da assemblati del tunnel, effettuata secondo normative interne Ferrari SpA.
Abstract. In the last years, industrial production of automotive chassis has gained a great evolution in design and technology, spurred by the need to achieve high performance and comfort, while ensuring both the safety of passengers and the environmental sustainability. State-of-the-art assembly lines, especially in top class segments, are designed to employ hybrid junctions on different chassis. Such complex process is based on the simultaneous adoption of welding, riveting and adhesive bonding technologies. The production systems design engages the development of specific automated devices and the cooperation of industrial robots and human resources. The solution of these issues involves the synergic action of various sectors of mechanical engineering, as metallurgy, design, and mechanical technology. Design of high flexibility production systems is another important issue: according to the viewpoint proposed by the authors, such systems are characterized by high structural and operational modularity, by parametric and standard design of solutions and components, by executive autonomy and rapid reconfiguration capability, thus simultaneously ensuring high quality of products and the complete control of processes. The present paper deals with the development and integrated design of the robotic adhesive bonding module in hybrid assembly lines for aluminum chassis, carried out in collaboration with the ALCOA group and SIR SpA. Experimental results are also presented, that refer to lap shear and peeling tests, carried out on specimens extracted from the chassis tunnel, according to Ferrari SpA internal standards.
2010
- Embedding detailed robot energy optimization into high-level scheduling
[Relazione in Atti di Convegno]
Vergnano, Alberto; C., Thorstensson; B., Lennartson; P., Falkman; Pellicciari, Marcello; C., Yuan; S., Biller; Leali, Francesco
abstract
Reduction of energy consumption is important for reaching a sustainable future. This paper presents a novel method for optimizing the energy consumption of robotic manufacturing systems. The method embeds detailed evaluations of robots’ energy consumptions into a scheduling model of the overall system. The energy consumption for each operation is modelled and parameterized as function of the operation execution time, and the energy-optimal schedule is derived by solving a mixed-integer nonlinear programming problem. The objective function for the optimization problem is then the total energy consumption for the overall system. A case study of a sample robotic manufacturing system is presented. It shows that there exists a possibility for a significant reduction of the energy consumption, in comparison to state-of-the-art scheduling approaches.
2010
- Hybrid Cost Automata Applied to Energy Optimization
[Relazione in Atti di Convegno]
B., Lennartson; C., Thorstensson; Vergnano, Alberto; P., Falkman; C., Yuan
abstract
For optimization of hybrid systems, the ordinary hybrid automatonis extended to include a local cost criterion in each location of thehybrid model. The extended model is called a hybrid cost automaton,where generally each local cost depends on the continuoustimestate trajectory in corresponding location, and each cost isupdated as long as its location is active. The total cost criterionis achieved by adding the individual costs from each active location,where the best route among alternative locations is selected inthe optimization. This model is used to achieve an energy optimalschedule for robot cells. Each robot operation including its energycost is then represented as a location, and a number of interactingrobots are modeled as a set of hybrid cost automata, one for eachindividual robot. The energy consumption for each robot operationis modelled and parameterized as a function of the operation’s executiontime, and the energy-optimal schedule is derived by solvinga mixed-integer nonlinear programming (MINLP) problem.
2010
- Metodi di progettazione integrata di sistemi automatici adattivi
[Relazione in Atti di Convegno]
Andrisano, Angelo Oreste; Faretra, Marco; Gherardini, Francesco; Guerra, Alessandro; Leali, Francesco; Pellicciari, Marcello; Pini, Fabio; Vergnano, Alberto
abstract
Le prestazioni dei moderni sistemi automatici di assemblaggio derivano sempre più dall’integrazione di apparati meccanici con attuatori programmabili, sensori, sistemi di elaborazione dati e complesse logiche di controllo. La disponibilità di tali tecnologie permette di affrontare nuove sfide tecniche ma comporta una rivoluzione nel modo di concepire meccanismi e macchine. I tradizionali modelli di progettazione, orientati alla definizione per funzioni degli apparati e strutturati con l’intervento sequenziale delle diverse aree di conoscenza dell’ingegneria, non permettono di sfruttare tutte le potenzialità delle diverse tecnologie coinvolte e di progettare comportamenti adattivi. È dunque necessario costruire nuovi metodi di progettazione che consentano di produrre sistemi in grado di interagire con l’ambiente circostante, di adattare autonomamente il proprio comportamento e di massimizzare e/o ottimizzare le prestazioni.
Il presente lavoro descrive un metodo per la progettazione integrata di sistemi automatici adattivi attraverso la modellazione e la prototipazione virtuale dei comportamenti. Il metodo segue un approccio sistematico e considera, a diversi livelli di dettaglio, l’evoluzione dinamica dei comportamenti sia tempo-continua che guidata da eventi discreti. L’integrazione delle conoscenze e delle tecnologie in un ambiente virtuale può portare all’evoluzione in nuovi principi risolutivi, alla creazione delle basi di conoscenza su cui sono basate le logiche adattive, ad avanzate strategie di sensorizzazione ed attuazione, all’ottimizzazione complessiva del sistema ed alla compressione dei tempi di sviluppo.
Questa memoria riporta infine l’applicazione del metodo proposto nella progettazione di un sistema di assemblaggio automatico.
2010
- Virtual prototype based method for hybrid reconfigurable assembly systems design in top class automotive industry
[Relazione in Atti di Convegno]
Andrisano, Angelo Oreste; Leali, Francesco; Pellicciari, Marcello; Pini, Fabio; Vergnano, Alberto
abstract
Changeability is mandatory for top class automotive industry to cope with new product development paradigms and demanding market. Hybrid Reconfigurable Assembly Systems (H-RMSs) address a customized flexibility on product families, given by coexistence or cooperation of human workers and robots. Key-issues for the effective design of harmonized hybrid assembly systems are: modularity; integrability of humans, machines and components; customization; convertibility; diagnosability of systems; and smart utilization of robots and skilled workers. Human and robotic tasks need a clear definition and allocation, for an effective enhancing of human dexterity and cognitive proactivity, together with robotic accuracy and strength. Virtual prototyping plays a strategic role within the H-RMS design optimization process, to explore different assembly setting and to interactively train operators but represents a challenging task and needs advanced tools. The present paper deals with the development of a Virtual Prototype based method for H-RMS design in top class automotive industry.
2009
- Artificial vision method for automatic robot code generation in robotic manufacturing for automotive industry
[Relazione in Atti di Convegno]
Andrisano, Angelo Oreste; Leali, Francesco; Pellicciari, Marcello; Vergnano, Alberto
abstract
Manufacturing operations performed by robotic systems in Mechanical Industry needprecision to achieve an high final quality on workpieces which are, generally,characterized by complex geometrical profiles, variable within small batch lots. Eachrobot movement is composed of hundreds of spatial points, calculated with respect toconstrains imposed by tool dimension and envelope. Consequently robot programmingrepresents a time consuming task, to be realized interrupting the system production. Anovel approach to the problem is discussed in the present paper. Artificial visiontechniques are applied to on-line reconstruct the workpiece profile and to calculate atailored tool path. A high resolution vision system moved by a preprogrammed roboticarm catches the workpiece. Images are elaborated and assembled to obtain a single highresolution view of the workpiece and to match the manufacturing features. Tool pathsare finally defined coherently with tool characteristics. The robot code is automaticallygenerated and transmit to the robot controller, ready to be executed. For an effectiveimplementation in Industry of the method developed, a graphic-based softwareapplication was realized. A tailored graphical interface was designed to guide the finaluser along the process and guarantee the best usability. State of the art hardware, visionlibraries and last generate anthropomorphic industrial robots were adopted to test themethod while an high performance engine head was chosen as benchmark forexperimental validation
2009
- Engineering Method for Adaptive Manufacturing System Design
[Articolo su rivista]
Andrisano, Angelo Oreste; Leali, Francesco; Pellicciari, Marcello; Vergnano, Alberto
abstract
Adaptive manufacturing systems achieve intelligence and adaptation capabilities through the close interaction between mechanics, electronics, control and software engineering. Mechatronic design of intelligent manufacturing behaviours is of paramount importance for the final performances of complex systems and requires deep integration between mechanical and control engineering. Virtual Commissioning environments offer engineers new opportunities for the design of complex intelligent behaviours and for the enhancement of the performance of adaptive manufacturing systems. This paper discloses a systematic design method focused on interdisciplinary behavioural simulations: Virtual Commissioning tools are used to virtually explore new solution spaces for an effective mechatronic optimization. The results, achieved by applying the method in reengineering a module of an automotive sensor manufacturing line, are finally presented.
2009
- Graphical control interface for dextrous hands in industrial robotics
[Relazione in Atti di Convegno]
Andrisano, Angelo Oreste; Leali, Francesco; Pellicciari, Marcello; Vergnano, Alberto
abstract
Industrial research in robotics is particularly focused in enhancing system flexibility andreconfigurability. Grippers and manipulation end effectors play a key role to achievesuch goals, evolving to complex mechatronic systems, whose capabilities appear as notyet fully exploited. Recent research studies investigate new generations of dextrous endeffectors, designed to emulate human hand architecture and behavior. Such systemsopen the way for innovative solutions in Industry but their use is still limited to researchlab or to service robotics. Despite that, dextrous hands seem to be mature enough to beused in industrial applications, usually more demanding in robustness and lifetimereliability within adverse environments. Thanks to the high number of degrees offreedom and to the advanced control electronics, dextrous hands could accomplishadvanced handling tasks as adaptive compliant assembly and could adopt intelligentbehaviors, sensitive to the operating scenario. To fully exploit the potentialities ofdexterous hands in Industry is necessary to develop specific interfaces to connect suchcomplex devices with anthropomorphic industrial robots. Dextrous hands programmingand control appear as key tasks in order to fully exploit their potentialities andperformances. The present work proposes a novel method, based on graphicalprogramming techniques, to create a clear and usable interface to introduce dextroushands in industrial robotics. The experimental results, obtained connecting a SDH-2(Schunk Dextrous Hand, Schunk GmbH & Co. KG) and a FANUC LR Mate 200iC robot, arefinally discussed.
2009
- Il Tecnopolo Regionale per la Meccanica della Provincia di Modena: strutture, organizzazione, obiettivi
[Relazione in Atti di Convegno]
Andrisano, Angelo Oreste; Leali, Francesco; Pellicciari, Marcello; Vergnano, Alberto
abstract
Il presente articolo descrive la struttura, l’organizzazione e gli obiettivi di ricerca industriale del Tecnopolo regionale per la meccanica della provincia di Modena, contestualizzandolo rispetto al sistema produttivo del territorio. Il Tecnopolo ha come principale finalità quella di rispondere efficacemente ai bisogni delle imprese attraverso la creazione di organi di gestione e di supervisione scientifica che consentano la condivisione delle problematiche di ricerca, la costituzione di gruppi di ricerca trasversali e la definizione di politiche comuni a più enti di ricerca ed il trasferimento tecnologico dall’Accademia all’Industria. Il Tecnopolo modenese persegue, dunque, obiettivi di ricerca che, senza perdere la propria natura scientifica, possano essere condivisi dalle realtà aziendali più intraprendenti ed attente allo sviluppo tecnologico, soprattutto da chi opera nei maggiori settori industriali dell’Emilia Romagna connessi con l’Alta Meccanica: automotive, meccatronica, micro e nanotecnologie, energetica, ICT, design industriale, biomedicale, ceramica. I maggiori ambiti d’azione riguardano la simulazione, la verifica e la simulazione di prodotti e processi industriali, a partire dai sistemi di trasmissione a ingranaggi fino ai motori ad alte prestazioni, dai componenti meccanici strutturali più raffinati ai processi di produzione robotizzati e automatizzati.
2009
- Metodi di visione artificiale in sistemi robotizzati per il settore automotive
[Relazione in Atti di Convegno]
Andrisano, Angelo Oreste; Pellicciari, Marcello; Leali, Francesco; Vergnano, Alberto; Pini, Fabio; Gherardini, Francesco; Faretra, Marco
abstract
Il presente articolo descrive un nuovo approccio di programmazione e guida robot capace di generare, automaticamente e in tempo reale, percorsi di lavorazione ottimizzati in funzione di singoli componenti. Tale metodo è stato validato sperimentalmente applicandolo al processo di sbavatura di una piccola serie di testate per motori a elevate prestazioni. Infatti i moderni sistemi robotizzati di produzione sono spesso impiegati in operazioni complesse su componenti che sono caratterizzati, specialmente nel settore automotive, da profili e geometrie multiformi, che variano radicalmente da un lotto produttivo a un altro e, nel caso di tecnologie che generano bave e difetti superficiali, anche all’interno di uno stesso lotto. Per ottenere l’elevata qualità richiesta dall’Industria, tali sistemi, molto ripetibili ma intrinsecamente poco precisi rispetto ai tradizionali centri CNC, richiedono la definizione di percorsi utensile composti da migliaia di punti e da articolati programmi robot, all’interno dei quali i parametri cinematici, dinamici e di lavoro vengono continuamente modificati. L’impiego di sistemi di guida robot a elevate prestazioni assume, dunque, un’importanza strategica nel processo di generazione del percorso utensile, specialmente all’interno di settori industriali nei quali è ancora largamente diffusa la pratica di generare manualmente, in autoapprendimento, le istruzioni di movimento dei robot e nei quali l’impiego di sistemi di programmazione offline CAD/CAE stenta ancora a trovare vasta applicazione. Di conseguenza, la fase di programmazione robot e il tempo a essa dedicato, rappresenta un aspetto che incide profondamente sulla reale flessibilità e produttività dei sistemi robotizzati.
2009
- Metodi e strumenti di prototipazione virtuale per il progetto e l’ottimizzazione di macchine e sistemi di automazione industriale
[Relazione in Atti di Convegno]
Andrisano, Angelo Oreste; Leali, Francesco; Pellicciari, Marcello; Faretra, Marco; Gherardini, Francesco; Pini, Fabio; Vergnano, Alberto
abstract
A seguito della drastica evoluzione del mercato il settore industriale della meccanica ha mostrato l’esigenza di interagire in modo sempre più efficace con il mondo della ricerca e dell’Università, con l’obiettivo primario di sviluppare prodotti e processi produttivi innovativi. Tale andamento si è concretizzato, da parte delle aziende, nell’orientamento al raggiungimento di un’elevata qualità durante tutto il ciclo di sviluppo prodotto/processo e nell’interesse alla (ri)-qualificazione dei propri addetti o all’acquisizione di nuove figure professioni di alto profilo. L’Università di Modena e Reggio Emilia, in collaborazione con altri Atenei emiliani e con la Regione Emilia Romagna ha operato con continuità, negli ultimi anni, per favorire e sostenere un efficace processo di trasferimento tecnologico dal mondo della ricerca verso il tessuto imprenditoriale. La costituzione del laboratorio SIMECH per la progettazione integrata e la simulazione, oggi confluito nella più ampia aggregazione INTERMECH, e la presentazione del progetto di creazione di un Polo Tecnologico per la Meccanica Avanzata e la Motoristica, con sede presso il Dipartimento di Ingegneria Meccanica e Civile di Modena, hanno costituito le tappe fondamentali di un’aggregazione orientata al consolidamento delle attività di ricerca di interesse del mondo produttivo e al loro rapido trasferimento industriale. Il presente articolo presenta due delle attività svolte negli ambiti del progetto, con particolare riferimento allo sviluppo di metodi e strumenti di prototipazione virtuale e all’ottimizzazione di macchine e sistemi per l’automazione industriale. Il primo caso presentato tratta lo sviluppo e la progettazione di una linea robotizzata di lavorazione ed assemblaggio di telai automobilistici in alluminio, svolta in collaborazione con SIR S.p.A., azienda leader nell’integrazione di sistemi industriali robotizzati, ed Alcoa Inc., importante gruppo specializzato nella produzione di telai, per conto di un’importante azienda automobilistica modenese. La seconda attività di trasferimento descrive il lavoro svolto in collaborazione con Dassault Systèms Italia nello sviluppo di metodi di progettazione di sistemi meccatronici adattativi di lavorazione basati su tecniche avanzate di Virtual Commissioning, attualmente implementati all’interno di alcuni importanti gruppi aziendali del territorio nazionale.
2009
- Progettazione orientata alla robustezza di prodotto e processo
[Articolo su rivista]
Andrisano, Angelo Oreste; Gherardini, Francesco; Pini, Fabio; Vergnano, Alberto
abstract
Progettare componenti per automobili di lusso ad elevate prestazioni implica la definizione di traguardi funzionali e prestazionali da perseguire con techiche orientate alla qualità totale del prodotto finale, valutata anche in termini di contenuti emozionali, senza tralasciare comunque la riduzione dei costi e l'ottimizzazione dei tempi e delle risorse aziendali.La multidisciplinarietà e la complessità del problema rende quindi necessario un approccio strutturato basato su metodi di ingegneria simultanea e sul coinvolgimento dei fornitori nelle attività di progettazione, almeno nelle fasi più critiche di definizione della catena di valore. Attraverso un approccio integrato basato sulla modellazione CAD/CAM e sull'adozione di tecniche SPC (Statistical Process Control) e FMEA (Failure Mode and Effect Analysis), si è giunti al miglioramento generale del meccanismo e al conseguente incremento della qualità di tutta la famiglia di torrette cambio ad esso correlata, soprattutto in termini di qualità percepita dall'utente finale. I risultati ottenuti hanno, inoltre, portato allo sviluppo di una soluzione specifica finalizzata al miglioramento della robustezza del prodotto e del processo produttivo sull'intero ciclo di vita.
2008
- Mechatronic design of adaptive manufacturing systems
[Relazione in Atti di Convegno]
Andrisano, Angelo Oreste; Leali, Francesco; Pellicciari, Marcello; Vergnano, Alberto
abstract
Adaptive manufacturing systems achieve intelligence and adaptation capabilities through the close interaction between mechanics, electronics, control and software engineering. Mechatronic design of intelligent manufacturing behaviours is of paramount importance for the final performances of complex systems and requires deep integration between mechanical and control engineering. Virtual Commissioning environments offer engineers new opportunities for the design of complex intelligent behaviours and for the enhancement of the performance of adaptive manufacturing systems. This paper discloses a systematic design method focused on interdisciplinary behavioural simulations: Virtual Commissioning tools are used to virtually explore new solution spaces for an effective mechatronic optimization. The results, achieved by applying the method in reengineering a module of an automotive sensor manufacturing line, are finally presented.
2008
- Metodi di progettazione integrata e simulazione di sottogruppi di macchine alternative
[Relazione in Atti di Convegno]
Andrisano, Angelo Oreste; Barbanti, Giovanni; Pellicciari, Marcello; Leali, Francesco; Faretra, Marco; Gherardini, Francesco; Pini, Fabio; Vergnano, Alberto
abstract
I moderni criteri di progettazione dei sistemi meccanici, spesso finalizzati a fronteggiare le elevate prestazioni delle macchine e la drastica riduzione dei costi e dei tempi di consegna, richiedono di considerare ed ottimizzare in tempi ridotti numerosi parametri funzionali all’interno di scenari operativi eterogenei, in cui gli aspetti strutturali, cinematici e dinamici non possono essere valutati indipendentemente. I metodi tradizionali di progettazione spesso affrontano questi aspetti in modo necessariamente approssimato e richiedono onerosi test su prototipi reali per la verifica e la messa a punto del sistema. La prototipazione virtuale utilizza diversi strumenti CAE (Computer Aided Engineering) per realizzare modelli di sistemi meccanici reali che tuttavia vengono ancora prevalentemente utilizzati come strumenti di verifica di sistemi già definiti con tecniche tradizionali. Nel presente lavoro si discute un metodo di progettazione che, pur fondandosi su solide basi di conoscenza tradizionali, permette di identificare con certezza i principali parametri progettuali su cui intervenire ed utilizza estesamente la prototipazione virtuale come strumento di progettazione. Si presenta inoltre la sua applicazione nella progettazione di un sistema per la sperimentazione di una macchina alternativa
2008
- Metodi e strumenti PLM per la progettazione integrata di sistemi meccatronici
[Relazione in Atti di Convegno]
Andrisano, Angelo Oreste; Gherardini, Francesco; Leali, Francesco; Pellicciari, Marcello; Pini, Fabio; Vergnano, Alberto
abstract
Lo sviluppo di prodotti e sistemi meccatronici implica attività multidisciplinari e concorrenti da svolgere con metodi e strumenti di sviluppo molto diversi tra loro. L’integrazione di tali attività è fondamentale per il raggiungimento degli obiettivi prestazionali ed il successo del prodotto e rappresenta uno dei maggiori problemi da risolvere a livello progettuale. Il trasferimento di conoscenze ed informazioni tra aree di competenza intrinsecamente diverse, da sincronizzare nei relativi processi di sviluppo, risulta il maggior limite da superare ed è spesso la causa principale di ritardi o di prestazioni non completamente ottimizzate. Nuovi ambienti di simulazione comportamentale sull’intero ciclo di vita permettono finalmente di disporre degli strumenti e tecnologie abilitanti per trasferire le reciproche conoscenze tra i diversi gruppi di lavoro e giungere in tempi ridotti ad una reale ottimizzazione dei sistemi. Gli autori hanno effettuato diverse esperienze nella progettazione di sistemi meccatronici nel campo della robotica ed automazione ed hanno ideato specifici metodi e strategie di impiego degli strumenti della piattaforma Delmia, che hanno permesso di sfruttarne le potenzialità raggiungendo vantaggi valutati e comparati rispetto allo stato dell’arte.
2007
- 3D MID Integrated Design for New Product Development in Advanced Mechatronics
[Relazione in Atti di Convegno]
Andrisano, Angelo Oreste; Leali, Francesco; Pellicciari, Marcello; Pini, Fabio; Vergnano, Alberto
abstract
TPMS (Tire Pressure Monitoring Systems) are required to provide high efficiency RF transmission, to be realized using components with reduced overall dimensions. Then, the design of TPMS antennas is a critical task, to be performed with accurate optimization activities based on intensive experimental development. In this field, MID technology can provide a strong strategic advantage since it can reduce the overall dimensions integrating different components and functionalities and, at the same time, permitting seamless fast prototyping, and customization, of different variants of the antenna layout.
In this paper it will be presented the integrated design and development (and the methods adopted) of a novel TPMS RF transmission unit, realized with LDS technology. In this activity, the design engineers used synergically several software tools to simulate and evaluate concurrently all the different problems involved.
The component geometries were designed in order to fulfil the structural and mechanical requirements, the molds were concurrently developed and the injection moulding process accurately simulated to validate the final shapes. At the same time, different design variants of the antenna were developed with intensive numerical simulations. A prototype mould was then quickly realized and specimens produced where, with LDS technology, the antennas lay out variants were manufactured. Several experimental testing on such prototypes were then performed in order to tune the 3D electromagnetic field simulation parameters (and be then able to perform further optimization studies on virtual prototypes). Finally a fast optimization of the antennas components was realized and the manufacturing processes tuned.
Such activities were jointly realized by DIMEC, Mechanical Engineering Department of the University of Modena researchers and Kontek Comatel R&D team
2007
- Design methods for intelligent robotic deburring cells
[Relazione in Atti di Convegno]
Andrisano, Angelo Oreste; Leali, Francesco; Pellicciari, Marcello; Pini, Fabio; Vergnano, Alberto
abstract
Cast iron parts deburring is a complicate and always more demanding task: it requires to realize an accurate 3D surface contouring, to be performed with an adequate tool stiffness and cutting power. At present time, cast iron parts production is characterized by small size lots of components which often have very different geometries. Moreover, it is easy to find that every single part of the same lot is quite different from the others, due to different burrs, varying in size and geometrical shape. Then cast iron parts deburring is a hard task which requires extreme flexibility. For this reason industrial robots seem to be the ideal solution; unfortunately the long time needed for programming the robot and the manufacturing cycle, together with the parts variability and components range reduces heavily the overall manufacturing efficiency and profitability. For this reason, novel intelligent manufacturing methods must be realized and implemented.
In the present paper it will be presented the integrated design and development of a new generation of cast iron parts robotic intelligent deburring and the engineering design methods adopted to achieve such results. The deburring of cast iron parts is performed by anthropomorphous robots with the integrated aid of vision systems, custom designed adaptive compliance tools and virtual prototypes of the cell itself, where it is possible to simulate all the different manufacturing tasks and automatically generate the code for the robotic cell numeric control. Using synergically all these tools and technologies it has been finally possible to overcome all the limits and problem of the state of the art. In fact, through the creation of a functional virtual prototype of the cell architecture, linked to different design and simulation environments, all the different operating scenarios can be simulated and all the information and data needed to solve the specific problems obtained. Exploiting synergically the performances of the vision system and the digital prototype it is possible to let the robot to interpret the operating scenario and to adopt proper intelligent behaviours, while, the realization of custom designed adaptive tools improves the cell overall performances. Furthermore, a design method for iron cast robotic deburring will be described.
2007
- Product and Process Robustness Enhancement for a Top Class Automotive Gearshift Tower
[Relazione in Atti di Convegno]
Andrisano, Angelo Oreste; Leali, Francesco; Pellicciari, Marcello; Pini, Fabio; Vergnano, Alberto
abstract
Automotive engineering is a challenging task for modern engineers. Requirements and technical specifications are more and more demanding, especially in relation with high performance and luxury class. Such aspects involve both functional and emotional aspects and pursues total quality, equally in product and manufacturing process. Moreover, a structured concurrent and co-design based engineering approach, involving the whole value chain, is required while cost need to be reduced, time saved and human and industrial resources spared.
The present paper deals with the design and manufacturing optimization of manual selection and clutch mechanism in a gearbox tower, realized to provide top class cars. Gearbox tower is the mechanical interface between drivers and engine transmission system in automotive applications. It has the primary function to permit driver selecting and shifting gears during vehicle march, to optimize engine running. Furthermore such mechanism has a central role in enhancing the overall market perception of the product and in transmitting to the customers good feelings about driving quality and car reliability, according to top class targets.
Robust design approach was primary followed, focusing on the continuous improvement of products and processes [1], [2].
Different existing solution for gearbox tower were firstly analyzed, performing a concurrent engineering analysis of each mechanical component from functional, productive and assembly points of view. Technical and technological aspects were discussed and compared through FMEA (Failure Mode and Effects Analysis) while an integrated CAD/CAM analysis (Pro/ENGINEER Wildfire 2.0) were carried out to optimize 5-axes CNC manufacturing. SPC (Statistical Process Control) were concurrently performed to maximize efficiency and process consistency.
A novel gearbox tower was finally designed. Three-dimensional parametric virtual prototype was realized and evaluated into its kinetic-dynamic characteristics within SolidWorks 2006 (Figure 1) and COSMOSMotion environments, in order to test the impact of different Computer Aided Tools inside a holonic and collaborative supply chain.
The method developed and the following studies leaded to the general enhancing of the gearbox project, especially in its more critic aspects. The gearbox tower family was optimized in its technical aspects and engineering performances respect to the state of the art. Moreover it was improved in terms of total quality perception from final users. Results obtained leaded to the develop of specific solutions focused in make the product and the related process more robust in the overall life cycle.