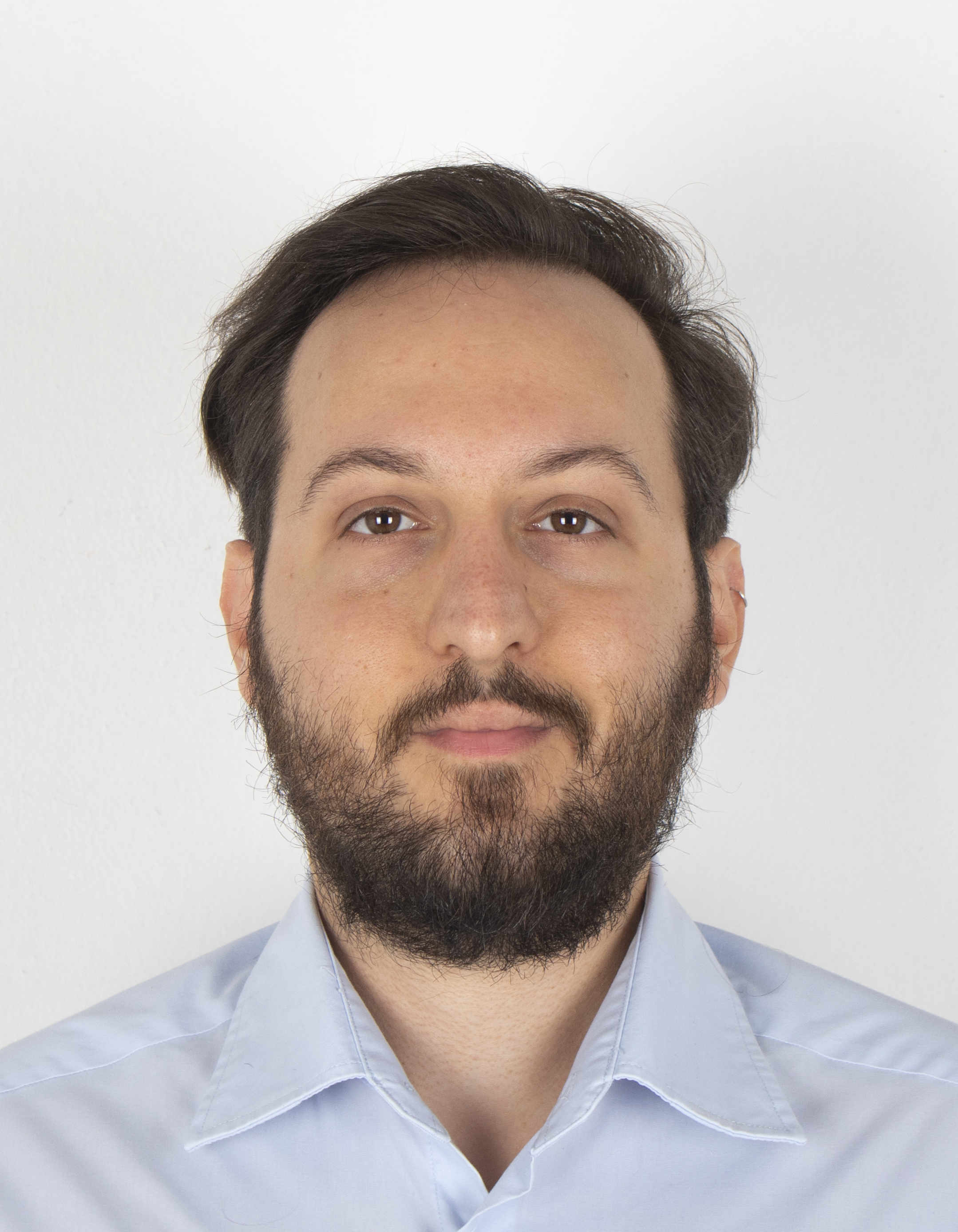 |
FABIO RENSO
Dottorando Dipartimento di Ingegneria "Enzo Ferrari"
|
Home |
Pubblicazioni
2024
- Numerical modelling of the cavitation damage in the conrod big end bearing of a high-performance internal combustion engine
[Relazione in Atti di Convegno]
Renso, Fabio; Giacopini, Matteo; Bertocchi, Enrico; Dini, Daniele
abstract
In this contribution a complementarity formulation for the solution of the elastohydrodynamic problem in the presence of cavitation is employed to investigate the tribological behaviour of the conrod big end bearing in a high-performance internal combustion engine. The continuous effort towards higher engine efficiencies, poses new challenges related to the increased specific loads to which engine components are subjected. In particular, the connecting rod big end bearing is subjected to both high loads and high relative velocity of the mating surfaces. Therefore, its tribological behaviour plays a crucial role. In fact, on one side, possible asperity contact pressures can produce wear of the interested components, and on the other side, a parallel possible cavitation of the lubricant can additionally damage the mating interfaces. Unfortunately for quantifying the cavitation damage, a universally established theory does not exist, even if it is well accepted that it is related to the sudden rapid implosion of the vapour bubbles near the surface. The precise investigation of this damage mechanism is usually neglected in big end bearing analysis since the implosion of the bubbles is difficult to quantify and it is not a standard output of any commercial software. Thus, in this work, a quantitative index previously proposed is reviewed and adopted to quantify the cavitation damage in a connecting rod big end bearing.
2023
- Finite Element Analysis of the Influence of the Assembly Parameters on the Fretting Phenomena at the Bearing/Big End Interface in High-Performance Connecting Rods
[Articolo su rivista]
Renso, Fabio; Barbieri, Saverio Giulio; Mangeruga, Valerio; Giacopini, Matteo
abstract
Fretting fatigue is a well-known and dangerous damage mode that occurs on the mating surfaces of mechanical components, mainly promoted by a combination of stress distribution, contact pressure distribution, and relative sliding (micro)motion between the surfaces. However, predicting this mechanism is challenging, necessitating specific studies for each assembly due to variable influences. This article presents a methodology for evaluating fretting fatigue damage at the contact between a titanium connecting rod big end and the bearing, adopting the Ruiz parameter as a quantifying damage index. For this purpose, a thermal-structural finite element model is prepared. In particular, the machining and assembly of the split conrod big end are simulated, considering thermal effects. A full engine cycle is first simulated, and results are used for identifying critical instants to be considered for accurate yet computationally efficient calculations. The dependence of fretting fatigue on three factors is studied: bearing crush, bolts tightening torque, and friction coefficient between the big end and the bearing. In summary, the damage increases with a higher crush and friction, while tightening torque has marginal effects. Following a 20% increase in crush height, a corresponding 10% rise in the Ruiz parameter is observed. Conversely, reducing the crush height by 20% leads to an approximately 8% decrease in the Ruiz parameter. When the influence of the bolt preload is taken into account, only a marginal 1% increase of the Ruiz parameter is recorded despite a 30% rise in preload. Evaluating the impact of the friction coefficient on the Ruiz parameter reveals an almost linear relationship. These findings suggest that adjusting the screw preload can enhance the hydrodynamic behavior of the bearing without exacerbating fretting. Furthermore, exploiting the linear correlation between Ruiz and the friction coefficient allows for the generalization of results obtained with specific coefficient values. This methodology can, therefore, serve as a valuable reference for adjusting different variables during the initial design phases of a four-stroke internal combustion engine’s dismountable connecting rod.
2023
- Influence of the crankshaft dynamic phenomena on the fatigue behaviour of a transmission chain in a hybrid power unit
[Relazione in Atti di Convegno]
Mangeruga, Valerio; Renso, Fabio; Raimondi, Francesco; Barbieri, Saverio Giulio; Giacopini, Matteo
abstract
This paper is part of an activity related to a specific hybridization process for an existing and commercialized
motorcycle engine. The electric motor is mechanically connected to the engine using the original valvetrain transmission
chain leading to a P0 hybrid architecture. The aim of this work is to analyse the structural behaviour of the chain now used
as torque transmission device. Although on one side the maximum torque of the electric motor determines a stress state on
the chain below its fatigue limit, on the other side, the dynamic behaviour of the system strongly influences the maximum
stress on the chain. In fact, the main source of load on the chain derives from the torsional oscillation of the system. Engines
rotational speed irregularity can be easily estimated through common analytical approaches which consider the contribution
of combustion and inertial forces on the instantaneous torque produced by the crank mechanism and the overall inertia of
the moving parts. However, more detailed lumped-parameters and Multibody dynamic models are here developed in order
to estimate the actual instantaneous engine speed taking into account the arising of possible high order vibration
phenomena. Specifically, the influence of the torsional vibration behaviour of the internal combustion engine isinvestigated
on the resulting stress on the chain. Finally, the structural chain integrity is assessed by performing a fatigue analysis
considering the actual operating conditions.
2023
- Investigation via Finite Element Analysis of the Influence of Boiling on the Thermo-Structural Behavior of the Engine Head of a High-Performance Combustion Engine
[Relazione in Atti di Convegno]
Piergiacomi, Andrea; Barbieri, Saverio Giulio; Renso, Fabio; Mangeruga, Valerio; Giacopini, Matteo
abstract
This paper presents a numerical methodology for studying the effect of boiling on the structural behavior of high-performance internal combustion engines. Boiling occurs when the portion of engine coolant in contact with hot walls reaches high temperatures and vapor bubbles form. While incipient vaporization of the coolant can promote additional cooling, excessive vapor can act as an insulator and lead to potentially dangerous high temperatures in the engine. Boiling is typically analyzed using Computational Fluid Dynamic Analyses, which are usually computationally intensive. In this study, the authors propose a Finite Element methodology that combines semi-empirical formulations, less demanding than Computational Fluid Dynamic models, with thermal Finite Element simulations to detect and manage boiling. Two different empirical formulations for boiling were employed, proposed by Garro and Chen respectively, and their results were compared. Three thermal analyses were conducted: the first neglected the effect of boiling, which leads to results inconsistent with the assumption of single-phase fluid, while in the second and third simulations, the occurrence of boiling and its effects were managed using the Garro and Chen formulations. The results showed a significant decrease in wall temperatures around the regions where boiling was detected and a parallel reduction of the thermal gradients inside the component. The two semi-empirical approaches for boiling estimation produced similar results, suggesting their substantial equivalence. Then, the temperature fields obtained were employed in structural Finite Element Analyses to evaluate the effects of boiling on the fatigue life of the engine head. In the structural analyses, the more uniform thermal field leads to a reduction of thermal deformations and to a different stress state, affecting the safety factor distribution. This methodology has the potential to be a suitable tool for detecting boiling and its effect during the early stages of engine design.
2023
- Numerical Investigation of the Dynamic Effects on the Fatigue Behaviour of a Transmission Chain in a Hybrid Power Unit
[Articolo su rivista]
Mangeruga, Valerio; Renso, Fabio; Barbieri, Saverio Giulio; Giacopini, Matteo; Raimondi, Franceco
abstract
2023
- Oil jets piston cooling: A numerical methodology for the estimation of heat transfer coefficients and optimization of the piston temperature field through a genetic algorithm
[Articolo su rivista]
Renso, Fabio; Giacopini, Matteo; Barbieri, Saverio Giulio; Mangeruga, Valerio
abstract
High-efficiency internal combustion engines need specific methodologies to be developed for the design improvement of the components. Predicting and reducing the thermal loadings on the parts are critical tasks to be addressed. This contribution focuses on the thermal management of the piston through oil jets. The operating temperature of the piston deeply affects its thermo-mechanical behavior, thus possibly jeopardizing the structural integrity of the component. The design of piston cooling jets is usually addressed through Computational Fluid Dynamics, which can guarantee accurate results, usually at a high computational cost. In this contribution, a faster tool is derived to grasp the effect of the cooling jets on the temperature of the piston. Empirical correlations are applied to predict the instantaneous heat transfer coefficients on the piston. The reciprocating motion of the piston is considered since it affects the interaction between the surface and the oil jets. Instantaneous coefficients are cycle-averaged and used to estimate the temperature of the piston through a Finite Element thermal analysis. Finally, an optimization code is developed to find the best jet configuration capable to minimize the temperature of the piston. This methodology is a powerful tool to select the optimal oil jet nozzles for piston cooling.